鋼結構及其材料焊縫內部缺陷(超聲方法)檢測
```
鋼結構及其材料焊縫內部缺陷(超聲方法)檢測
隨著工業技術的不斷發展,鋼結構在建筑、機械、交通等領域得到了廣泛應用,其優異的強度、穩定性以及可循環使用的優點使其成為現代社會不可或缺的材料。然而,鋼結構的安全性和穩定性在很大程度上取決于焊縫的質量,而焊縫內部缺陷的不及時檢測和修復,可能導致災難性的后果。因此,采用高效、可靠的無損檢測手段來確保焊縫質量,是保障鋼結構安全的重要措施。超聲檢測方法憑借其靈敏度高、效率高以及覆蓋范圍廣的特點,成為檢測焊縫內部缺陷的主要手段之一。
焊縫質量與其內部缺陷
焊縫是鋼結構中承載和連接的重要部分,而焊接過程是一個復雜的熱力學過程,很容易因焊接參數的變化或外界因素的干擾產生缺陷。常見的焊縫缺陷包括裂紋、氣孔、夾雜物、不完全熔合和未焊透等。這些缺陷危及鋼結構的承重能力和疲勞性能,甚至可能導致焊縫局部失效或整個結構的崩塌。
尤其在高應力或惡劣環境下工作的大型鋼結構,例如橋梁、海上鉆井平臺和核電站等,焊縫質量顯得尤為關鍵。這些場景下,焊縫內部的微小缺陷可能因應力集中逐漸擴展,進而釀成嚴重破壞。因此,預防性維護和焊縫缺陷的早期檢測對鋼結構的安全運營起到重要作用。
超聲檢測方法的原理
超聲檢測是一種基于超聲波傳播原理的無損檢測技術,其基本原理是利用超聲波在材料中的傳播特性來探測缺陷。超聲波是一種頻率高于20 kHz的彈性波,當其以一定的方向和速度傳播到介質中的不連續點(如孔洞、夾雜物或裂紋)時,會發生部分聲波的反射、折射和散射。通過接收這些反射信號并分析其幅度、相位和到達時間,可判斷缺陷的位置、形狀和大小。
在焊縫檢測中,超聲波檢測的實施步驟通常包括:選擇適當的探頭,調節儀器參數,使超聲波以指定的角度發射到焊縫區域;接收從缺陷或其他界面反射的回波信號;將信號轉換為可視化的波形顯示在屏幕上供分析。這一過程既高效又精確,可滿足大多數工業需求。
超聲檢測方法的優勢
相比其他無損檢測方法,如射線檢測、磁粉檢測和滲透檢測,超聲檢測在焊縫檢測中有許多顯著的優勢。
靈敏度高
超聲波對于材料內部的細微不連續性,如微小裂紋或氣孔,具有極高的靈敏度。這使得超聲檢測能夠發現早期的焊縫缺陷,從而及時采取修復措施,避免缺陷擴展。
檢測深度大
超聲波具有良好的穿透能力,尤其在鋼材等致密材料中,可達到幾十厘米甚至更深的穿透深度。因此,在厚壁焊縫或難以接近的區域,超聲檢測比其他方法如射線檢測更為有效。
即時結果與便攜性
超聲檢測是一種實時檢測技術,檢測結果可以立即顯示并進行分析。這種即時反饋使操作人員能夠快速定位和評估缺陷。此外,便攜式超聲檢測設備體積小、重量輕,特別適用于現場檢測。
超聲檢測方法的局限性
盡管超聲檢測方法有許多優點,但其也存在一些局限性。例如,超聲檢測需要經驗豐富的操作人員對缺陷信號進行分辨和解釋,避免誤報或漏報。此外,接頭表面粗糙、超聲波耦合介質不足等因素可能會影響檢測結果的準確性。在某些情況下,如復雜焊縫區域,超聲波的傳播路徑可能受到限制而難以得到精確的回波信號。
另一個挑戰是設備和探頭的配置以及檢測方案的設計。不同類型的焊縫和缺陷需要選用不同的探頭頻率和波型,還需設置適當的掃描方式,這對檢測技術的系統性和針對性提出了更高要求。
超聲檢測的實際應用與發展
超聲檢測廣泛應用于建筑、石化、電力和橋梁等工業領域。在艦船制造中,大型鋼結構焊縫的檢測是不可或缺的一環;在航空工業中,精度要求高的薄壁焊縫也離不開超聲檢測;在核電站和壓力容器中,超聲檢測更是全面應用于壽命評估與安全保障。
隨著科技的進步,超聲波檢測技術也在不斷升級。相控陣超聲檢測(PAUT)和全聚焦法(TFM)作為現代超聲技術的新發展,通過多通道同步控制技術和復雜的信號處理算法,能夠提供更加清晰的3D圖像,使檢測結果更加直觀。此外,人工智能和大數據技術也正逐步融入超聲檢測領域。利用智能算法處理檢測數據,可以實現缺陷信號的自動化識別和分類,從而提高檢測效率和準確性。
鋼結構及其材料的焊縫缺陷檢測對保障結構安全至關重要。超聲檢測作為一種成熟的無損檢測技術,憑借其高靈敏度、高穿透性及實時性等優勢,在焊縫內部缺陷的早期識別和定位中發揮著重要作用。然而,技術的進一步發展仍需突破其現有局限性,特別是在復雜結構和深層缺陷的精確檢測領域。借助齊全的硬件設備、算法優化以及人工智能技術的引入,超聲檢測方法將更趨完善,并在未來的工業應用中發揮更大價值。
```
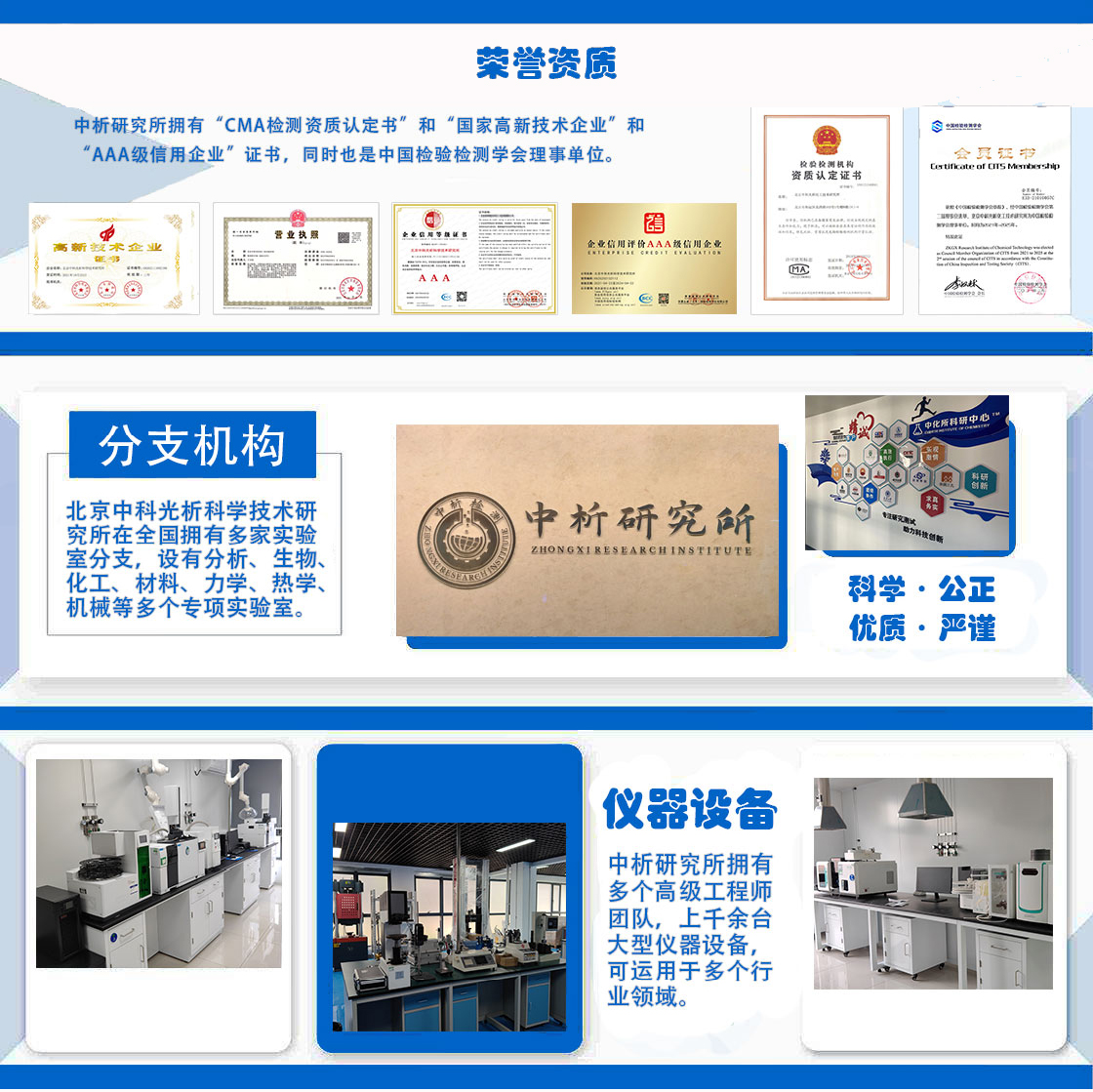
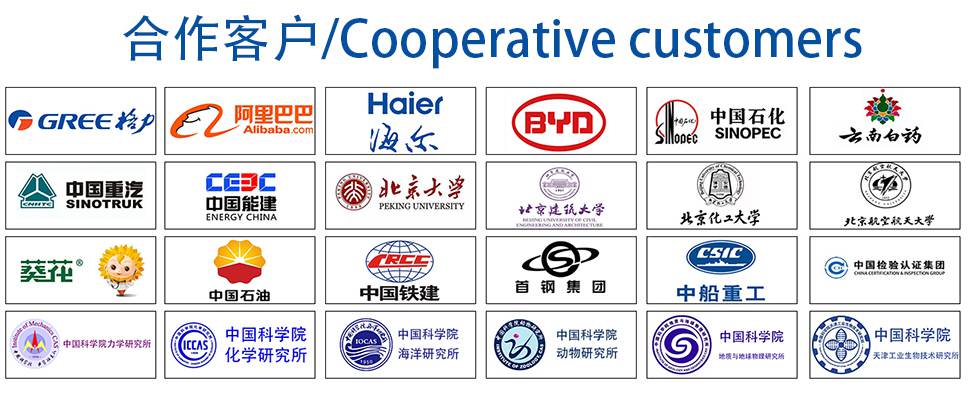