飛機地面加油和排油用橡膠軟管及軟管組合件檢測的重要性
飛機地面加油和排油用橡膠軟管及軟管組合件是航空燃油輸送系統的核心部件,其性能直接關系到飛行安全和運營效率。由于這些軟管長期暴露于極端溫度、化學腐蝕、機械應力等復雜環境中,任何結構缺陷或性能衰退都可能導致燃油泄漏、靜電積聚甚至火災風險。因此,定期開展全面、科學的檢測項目至關重要,以確保軟管滿足國際航空標準(如FAA、ISO等)和行業規范(如SAE AS1339)。
關鍵檢測項目及技術要點
1. 結構完整性檢測
通過目視檢查、尺寸測量和X射線成像技術,評估軟管的內襯層、增強層和外覆層是否存在裂紋、磨損或變形。重點檢測接頭部位的密封性,確保無滲漏風險。
2. 耐液壓性能測試
模擬實際工作壓力(通常為3-10 MPa),在靜態和脈沖壓力下驗證軟管的抗壓能力。檢測內容包括壓力保持性、膨脹率及爆破壓力,確保軟管在極端工況下的穩定性。
3. 導電性能驗證
使用電阻測試儀測量軟管整體電阻值(需≤10^4 Ω/m),確認靜電導出能力符合MIL-DTL-25516等標準,避免燃油輸送過程中靜電積聚引發燃爆事故。
4. 材料老化與耐介質性分析
通過熱氧老化試驗、耐油性測試(ASTM D471)和臭氧暴露試驗,評估橡膠材料在長期接觸航空燃油、潤滑油及環境因素下的劣化程度,確保材料壽命≥5年。
5. 低溫柔韌性與高溫耐受性測試
在-40℃低溫環境中進行彎曲試驗,驗證軟管在寒冷條件下的抗脆裂能力;同時進行150℃高溫曝露測試,檢測材料軟化或變形情況。
6. 動態彎曲疲勞試驗
模擬地面加油車的頻繁移動場景,通過機械臂進行萬次以上彎曲循環測試,監測外層橡膠龜裂、增強層斷裂等疲勞失效現象。
檢測周期與注意事項
建議每6個月進行一次全面檢測,高頻使用場景需縮短至3個月。檢測時需注意清潔管腔殘留燃油、避免機械損傷,并嚴格記錄批次編號和檢測數據。對于已發現局部損傷的軟管,禁止采用修補方式復用,必須按照適航要求強制報廢。
通過上述系統化檢測,可有效預防因軟管失效導致的航空事故,同時降低燃油污染和運營成本。航空公司及地勤單位應建立完善的檢測檔案,并優先選擇通過NADCAP認證的第三方檢測機構合作。
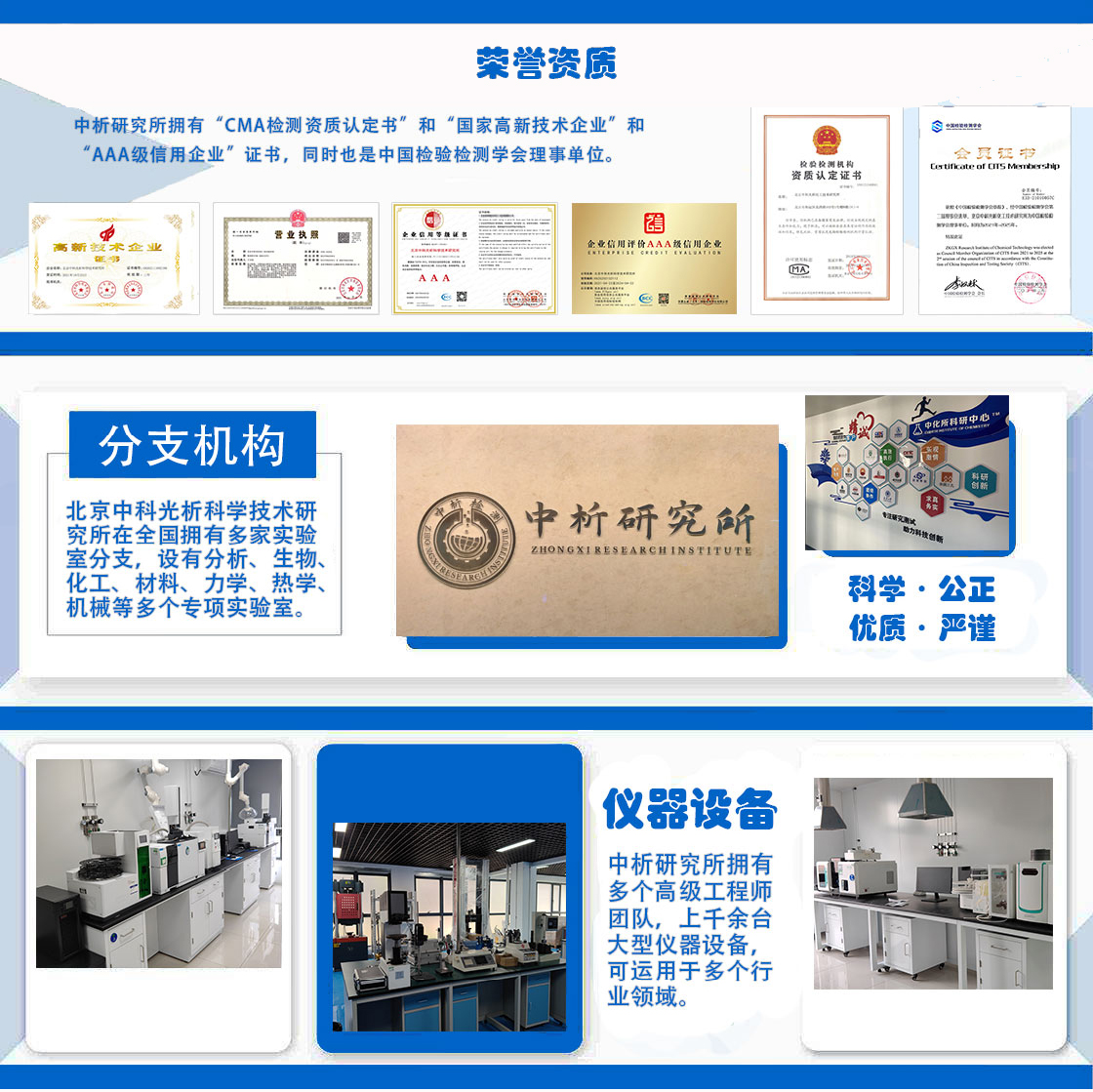
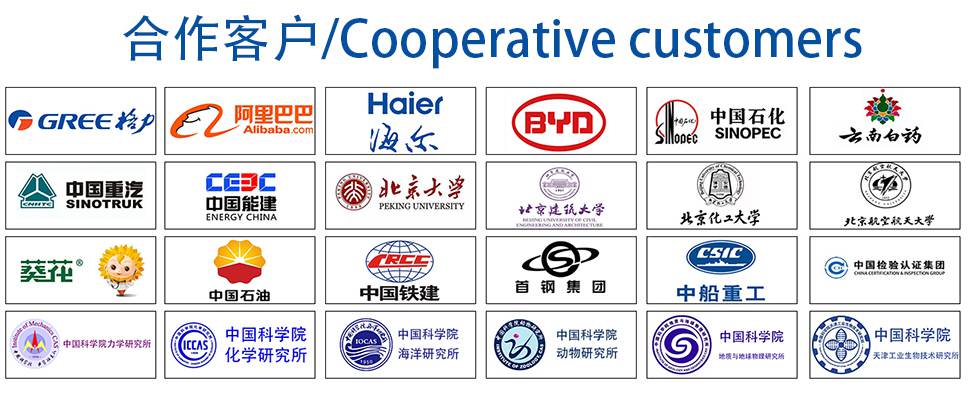