平衡機檢測的核心作用與意義
平衡機檢測是工業制造領域中保障旋轉設備運行穩定性的關鍵技術,廣泛應用于電機、風機、渦輪機、汽車零部件等核心部件的質量控制。通過精準檢測旋轉體的不平衡量,可有效降低設備振動、減少噪音、延長使用壽命,并避免因失衡導致的機械故障或安全事故。隨著現代工業對設備精度要求的提高,平衡機檢測已成為機械加工、汽車制造、航空航天等行業不可或缺的質量控制環節。
平衡機檢測的主要項目及技術要點
1. 靜平衡檢測
靜平衡檢測主要針對盤狀或短軸類工件,通過在靜態狀態下測量質量分布差異。檢測時將被測物體置于水平軌道或靜平衡架上,觀察其自然靜止狀態下的重力分布情況。當物體重心與旋轉軸線重合時達到靜平衡狀態,否則需通過配重法或去重法進行校正。該檢測適用于低轉速、軸向長度較小的旋轉體。
2. 動平衡檢測
動平衡檢測針對長軸類或高速旋轉設備,需在動態狀態下完成測量。通過驅動系統使工件以實際工作轉速旋轉,利用傳感器采集振動信號,計算不平衡量的相位與大小。現代動平衡機普遍采用雙面校正法,可同時檢測和修正兩個校正平面的不平衡量,精度可達0.1g·mm/kg級別。
3. 轉速適應性測試
該檢測驗證平衡機在不同轉速下的測量穩定性。通過設定階梯式轉速變化(如300-3000rpm分段測試),觀察測量系統的重復性與線性度。關鍵指標包括轉速波動率(應≤±1%)和信號采集同步性,確保在寬轉速范圍內保持檢測精度。
4. 傳感器系統校準
振動傳感器和相位檢測器的定期校準至關重要。采用標準轉子進行系統標定,驗證傳感器靈敏度、頻率響應特性及相位角測量精度。根據ISO21940標準,校準周期不超過6個月,環境溫度變化超過10℃需重新校準。
5. 夾具精度驗證
專用夾具的同心度誤差直接影響檢測結果。使用三坐標測量儀檢測夾具的徑向跳動(應≤0.01mm),同時需模擬裝夾過程驗證重復定位精度。對于異形工件,還需進行動態夾持力測試,確保旋轉過程中不發生位移。
6. 動態響應分析
通過頻譜分析技術評估設備振動特性,檢測是否存在共振風險。結合FFT(快速傅里葉變換)分析振動信號的頻率成分,識別由不平衡、軸彎曲或裝配誤差導致的異常振動源,為綜合質量評估提供依據。
檢測標準與質量管控
平衡機檢測需嚴格遵循ISO1940(剛性轉子平衡精度等級)、API617(石油化工設備標準)等行業規范。企業應建立完整的檢測檔案,記錄初始不平衡量、校正方案及最終殘余不平衡量,確保可追溯性。對于關鍵設備,建議每運行800-1000小時后進行復檢,動態監測平衡狀態變化。
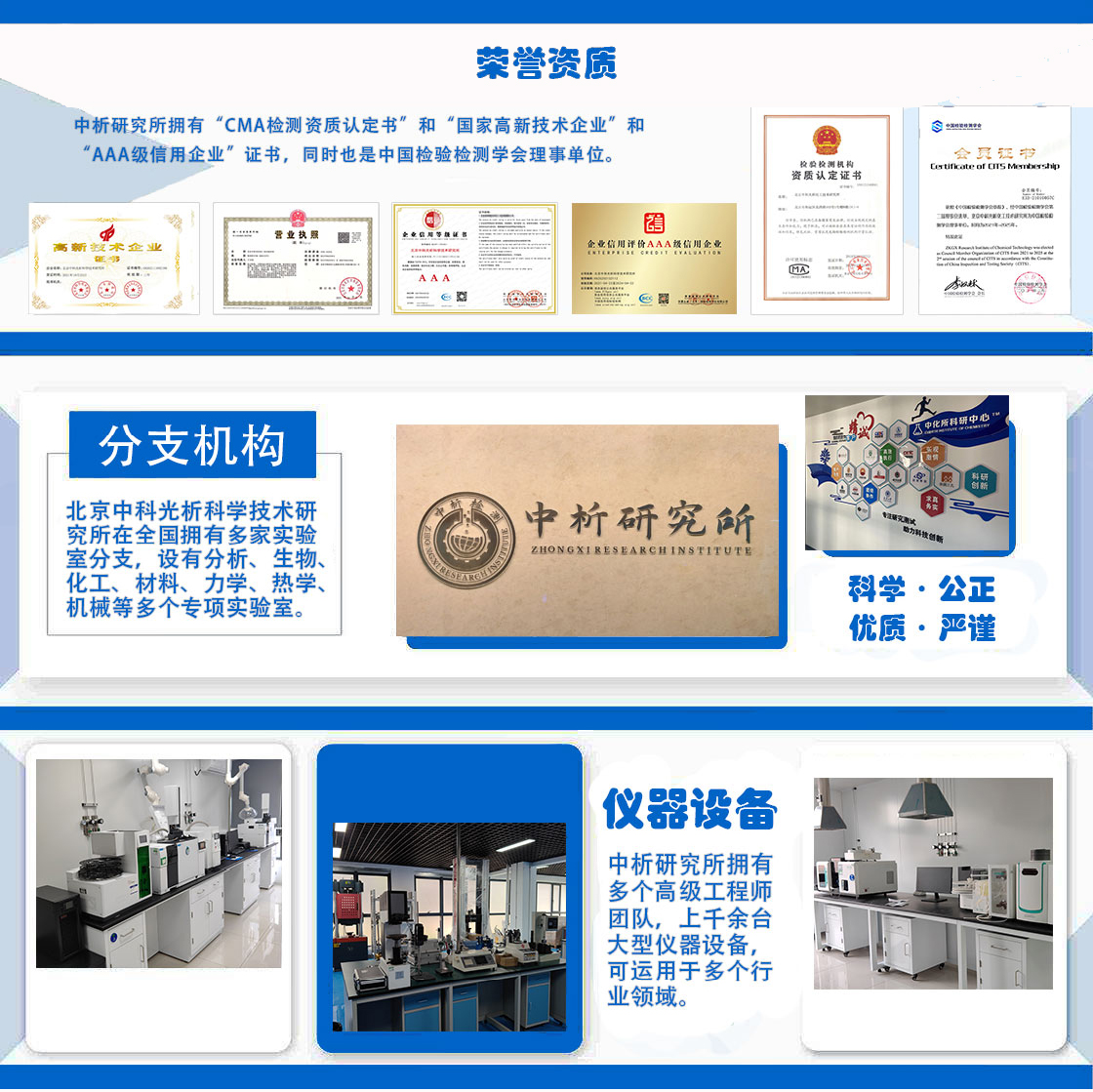
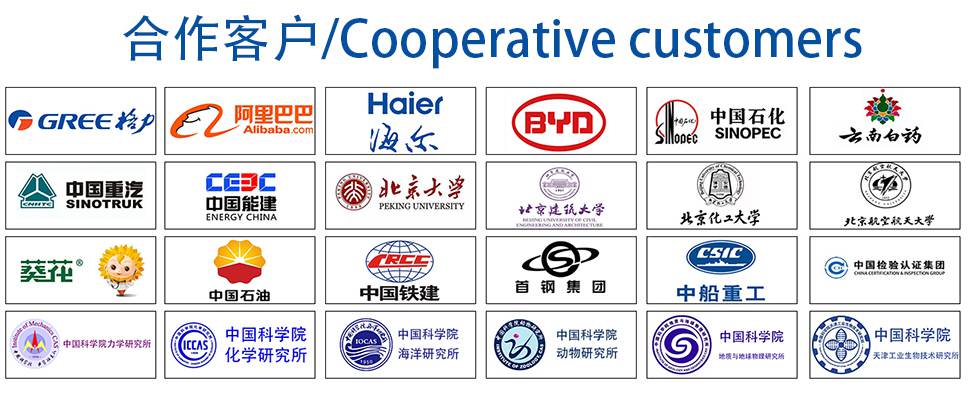