煤礦重要用途在用鋼絲繩檢測的重要性
煤礦生產中,提升機、運輸機等設備使用的鋼絲繩是保障礦井安全運行的核心部件。其長期承受高強度載荷、惡劣環境(如潮濕、腐蝕性氣體)以及動態疲勞作用,易出現斷絲、磨損、銹蝕等隱患。一旦鋼絲繩失效,可能引發斷繩墜罐、物料墜落等重大事故,直接威脅人員生命安全和礦井正常生產。因此,對煤礦重要用途在用鋼絲繩開展系統性檢測,既是國家《煤礦安全規程》的強制要求,也是企業落實安全生產主體責任的關鍵環節。
核心檢測項目及技術要求
1. 外觀與結構檢查
采用目視、放大鏡及卡尺對鋼絲繩表面進行全長度檢查,重點記錄斷絲數量(單捻距內斷絲不得超過總絲數10%)、磨損量(直徑減小率需≤10%)、銹蝕程度(銹蝕面積占比分級評定)及變形(如籠狀畸變、繩股擠出)情況。檢測需覆蓋繩端固定裝置和連接部位。
2. 直徑測量與捻距分析
使用專用繩徑卡規在無張力狀態下分段測量,對比公稱直徑計算實際縮減率。同時測量捻距長度(相鄰股峰間距),若偏差超過原始值±5%,則表明結構穩定性下降。檢測數據需繪制趨勢圖以評估劣化速度。
3. 內部損傷無損檢測
應用磁記憶檢測(MMT)或漏磁檢測(LF)技術,通過磁場變化識別內部斷絲、銹坑及金屬截面積損失。對于多層股鋼絲繩,需采用旋轉式探頭確保100%覆蓋率。檢測系統應滿足MT/T970標準要求,缺陷信號需經專業軟件解析并生成三維損傷圖譜。
4. 力學性能測試
截取代表性繩段進行破斷拉力試驗(保留系數應≥1.2倍最大靜載荷),同步測試彎曲疲勞壽命。對于已使用2年以上的鋼絲繩,還需通過金相分析評估材料晶界腐蝕情況,確保抗拉強度保留率≥90%。
5. 潤滑狀態評估
檢測周期與結果處理
根據《煤礦安全規程》第413條規定,提升鋼絲繩必須每日由專職人員檢查1次,每月進行1次全面檢測,新投用或經大修的鋼絲繩需在初始24小時內完成首次張力測試。檢測發現單捻距斷絲數超標、直徑減小率>10%或剩余強度系數<5.0時,必須立即停止使用并更換。所有檢測數據應錄入智能化管理系統,實現壽命預測與預防性維護決策。
技術發展動態
當前行業正推進基于物聯網的在線監測系統應用,通過集成光纖傳感、聲發射檢測等技術,實現鋼絲繩應力分布、損傷演化的實時監控。同時,人工智能算法開始用于缺陷模式識別,檢測準確率可達98%以上,大幅提升了安全隱患的早期預警能力。
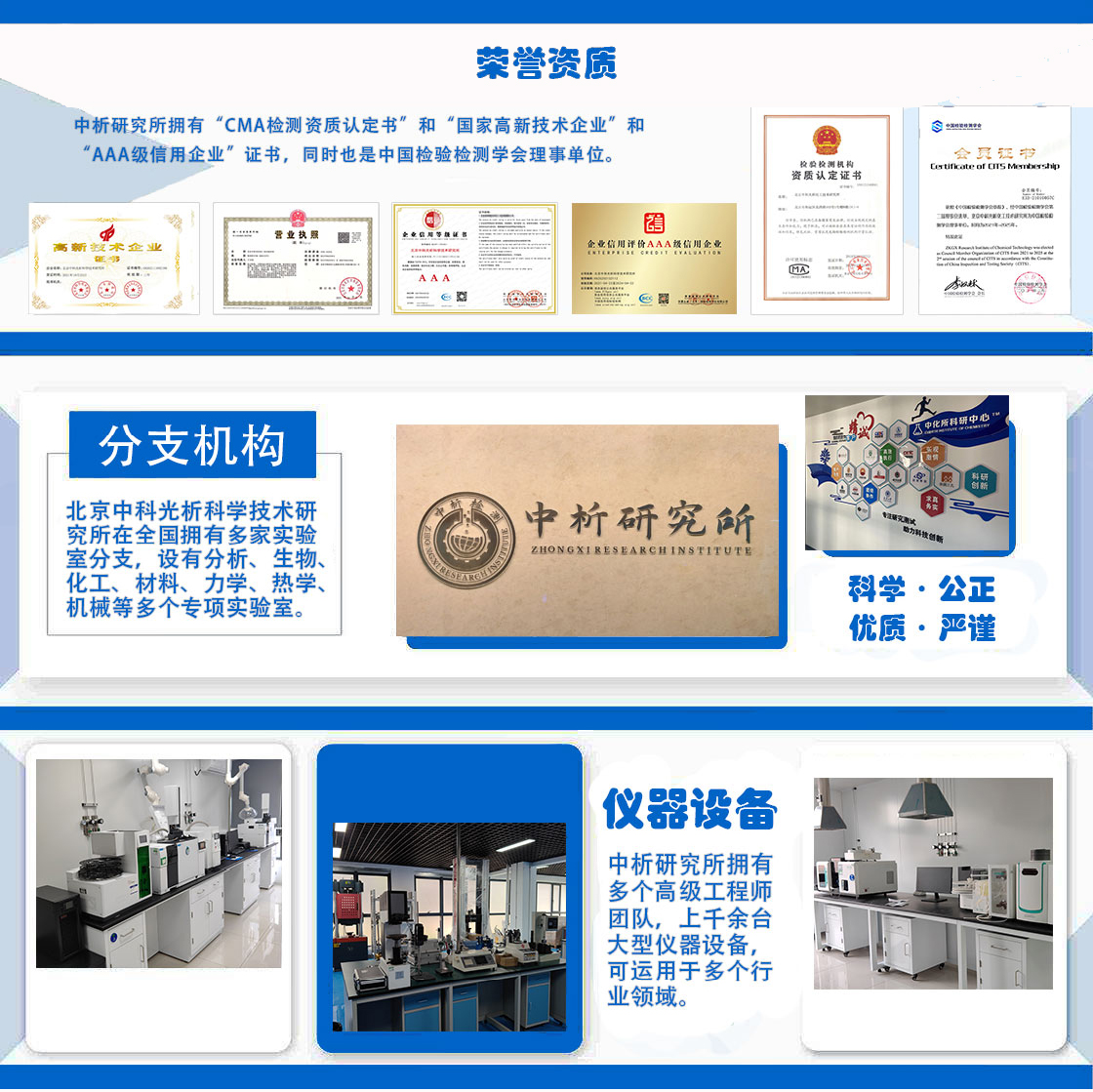
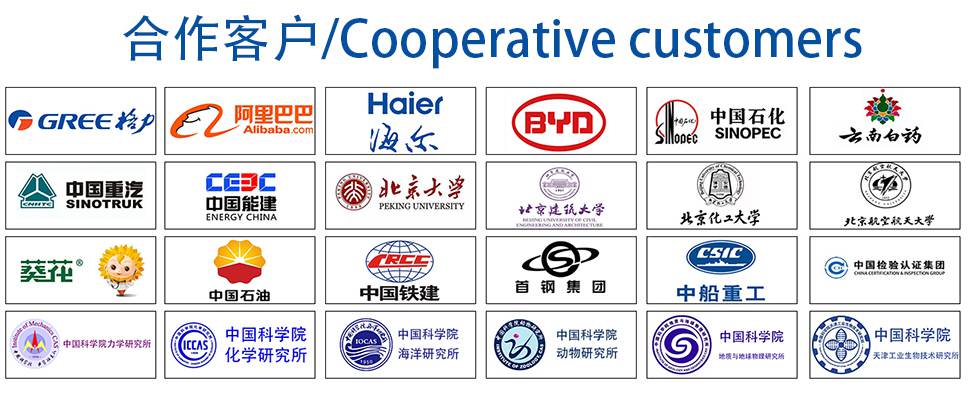