拒油性抗碳氫化合物試驗檢測的意義與核心要求
在工業制造、醫療防護及航空航海等領域中,材料對油性液體和碳氫化合物的抵抗能力直接影響其性能與安全性。拒油性抗碳氫化合物試驗檢測通過模擬實際使用環境中的油污、燃料或其他烴類物質接觸場景,驗證材料的防護效能。近年來,隨著環保法規的嚴格化及工業材料升級需求,該項檢測已成為化工、紡織、汽車等行業質量控制的核心環節。通過科學評估材料的表面張力、滲透時間和耐久性,可有效避免因材料失效導致的污染泄漏、設備腐蝕或人員健康風險。
檢測項目與關鍵技術指標
1. 表面潤濕性測試
通過液滴接觸角測量分析材料表面的拒油性能。測試時采用標準碳氫化合物液體(如礦物油、正己烷)滴落于材料表面,觀察液體擴散程度。接觸角大于90°時表明材料具備基礎拒油性,角度越大則防護效果越優。
2. 滲透時間測定
在恒定壓力條件下,記錄油性液體穿透材料所需時間。試驗參照AATCC 118、ISO 14419等標準,使用不同粘度的碳氫化合物(如柴油、潤滑油)進行分級測試,時間閾值需達到行業規定等級(如6級對應≥120分鐘)。
3. 化學抗性耐久性測試
對材料進行多次污染-清潔循環實驗,檢測拒油性能的穩定性。包括高溫老化、機械摩擦處理后復測接觸角及滲透時間,評估材料在長期使用或極端環境下的防護能力衰減情況。
4. 微觀結構分析
采用掃描電鏡(SEM)或紅外光譜(FTIR)觀察材料表面涂層完整性及化學結構變化。碳氫化合物侵蝕可能導致材料孔隙率增加或功能基團破壞,微觀檢測能精準定位失效原因。
檢測標準與行業應用
目前國際通行的拒油性抗碳氫化合物檢測標準包括美國AATCC 118、ASTM F739,以及歐盟EN 374-3等。醫療防護服需通過ISO 22612抗礦物油滲透認證,工業密封件則依據API 6A標準進行高壓烴類耐壓測試。檢測數據直接用于產品分級認證,例如防護服達到Type 4級(防液態化學品)需滿足特定滲透閾值。
技術難點與未來發展趨勢
當前檢測面臨的主要挑戰在于模擬真實復雜工況(如混合油污、動態壓力)。未來將向智能化檢測設備(自動潤濕分析儀)、多因子耦合測試(溫度+壓力+化學腐蝕同步評估)方向突破,同時結合AI算法預測材料壽命,推動新型氟碳涂層、納米復合材料的研發進程。
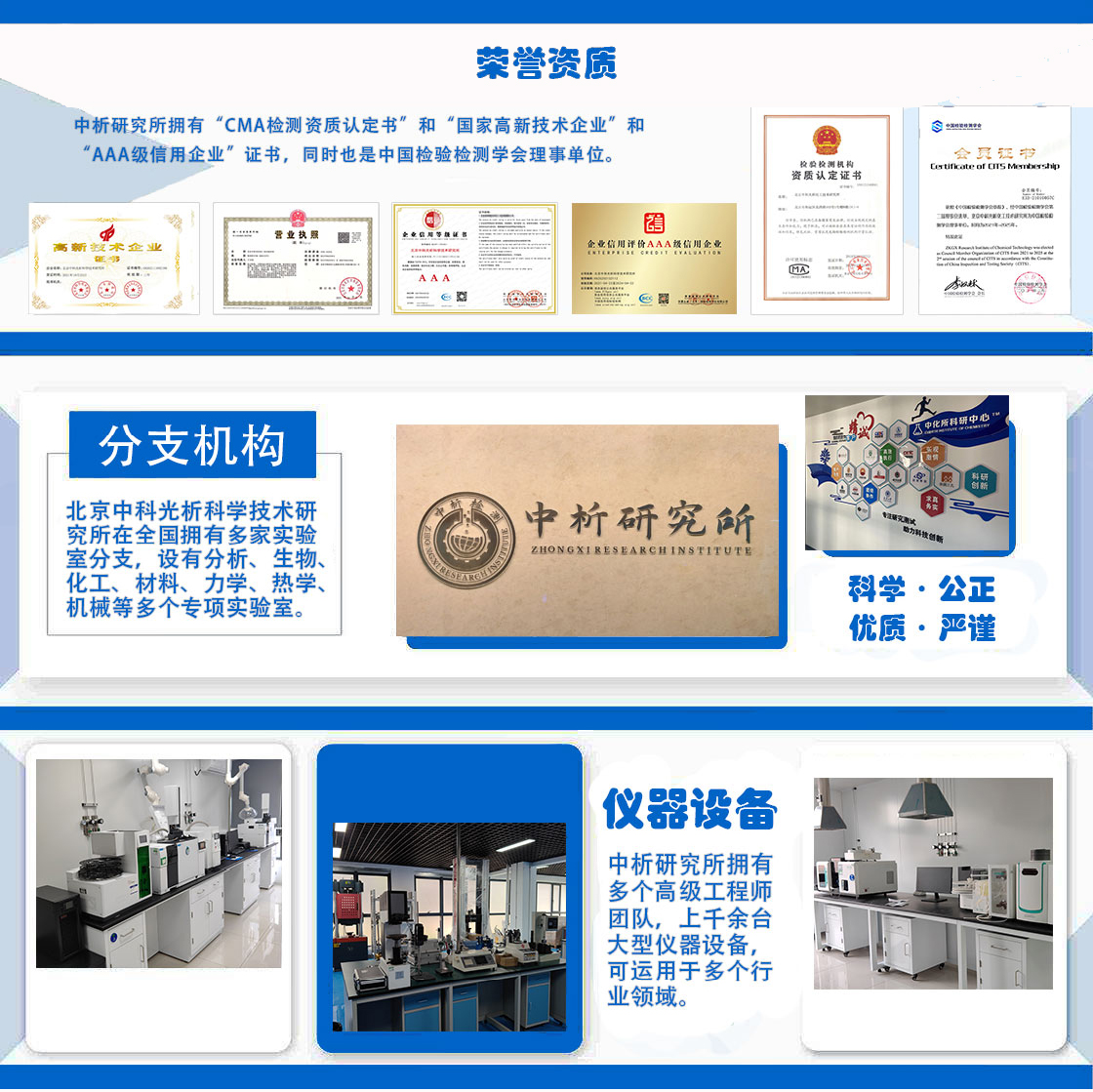
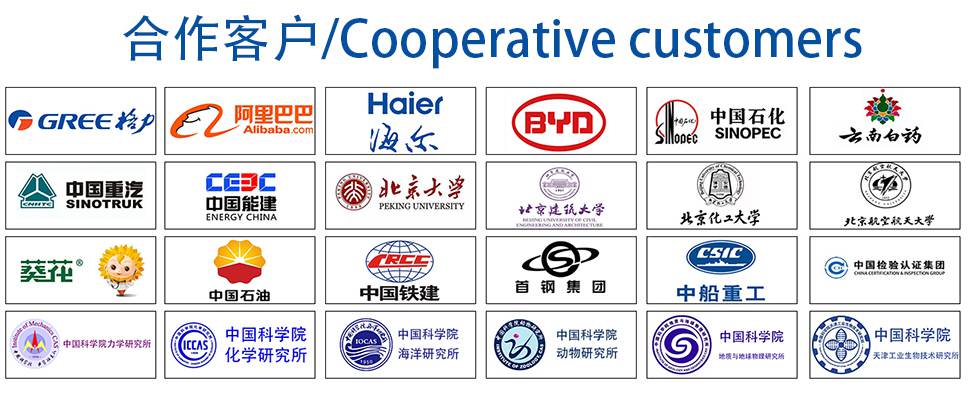