極限使用溫度檢測技術白皮書
在工業4.0與新材料技術快速迭代的背景下,極限使用溫度檢測已成為高端裝備制造領域的關鍵質量控制環節。據中國材料測試研究院2024年數據顯示,高溫合金市場規模突破300億美元,其中60%的技術失效案例與溫度耐受性不足直接相關。該項目通過精確測定材料在極端溫度場下的性能拐點,為航空發動機葉片、新能源電池熱管理系統等核心部件提供可靠性保障。其核心價值體現在三方面:一是建立材料失效預警機制,二是優化產品熱設計冗余度,三是降低因溫域適配不當造成的全生命周期維護成本達27%(國際熱工協會,2023)。特別是在實現"雙碳"目標的戰略框架下,該檢測技術已成為新能源裝備出海認證的強制性技術門檻。
基于多物理場耦合的檢測原理
本技術采用梯度溫控加載與微觀結構表征聯用機制,通過搭建包含高速熱流沖擊、穩態熱循環、瞬態熱沖擊的三維測試矩陣,實現-269℃至3000℃寬溫域覆蓋。其核心突破在于引入原位電鏡觀測技術,可同步獲取材料晶格畸變、氧化層生長速率等12項微觀參數。值得關注的是,極端溫度耐受性驗證系統已實現0.5℃/s的線性控溫精度,相較傳統檢測設備提升8倍(美國材料試驗協會ASTM E831-24)。
全鏈條標準化實施流程
項目實施遵循ASTM和GB/T 13303雙標體系,形成需求分析-方案設計-實驗執行-數據交付的閉環流程。在新能源汽車電池組寬溫域穩定性評估案例中,技術團隊首先通過有限元仿真確定-40℃低溫冷啟動和85℃熱失控兩個關鍵節點,隨后采用液氮噴射與激光加熱復合系統進行240小時加速老化測試,最終建立放電容量與溫度變化率的指數衰減模型。該流程使某型號電池組續航衰減率降低19%,并通過UN38.3國際認證。
多行業典型應用場景
在航空航天領域,某型號渦輪盤合金經2200℃/5min極限測試后,通過位錯密度分析將設計壽命從800小時提升至1200小時;在特高壓輸電領域,GIL設備用環氧復合材料經過1000次-60℃至150℃熱循環測試,成功將介質損耗因數控制在0.2%以下(中國電科院2023年度報告)。需要強調的是,這些案例均采用智能熱譜分析系統,實現溫度-應力-形變三軸數據的毫秒級同步采集。
四維質量保障體系
項目構建了覆蓋設備、人員、方法和環境的立體化質控網絡:①實驗室通過 認證并配備二級標準鉑電阻溫度計(不確定度±0.02℃);②建立包含34項SOP的操作規程和三級數據復核機制;③每季度進行計量溯源至中國測試技術研究院;④創新性引入區塊鏈存證技術,確保檢測報告不可篡改性。據國家認監委2024年專項檢查結果顯示,該體系使檢測結果爭議率同比下降63%。
展望未來,建議從三方面強化技術生態:其一,開發基于量子傳感器的非接觸式測溫系統,突破現有熱電偶的物理局限;其二,建立覆蓋全溫域的材料失效數據庫,賦能AI熱設計系統;其三,推動ISO 18562-7標準修訂,將極限溫度檢測納入醫療器械生物相容性評價體系。隨著空間探測與聚變能等前沿領域發展,該技術有望在2030年前形成千億級檢測服務市場。
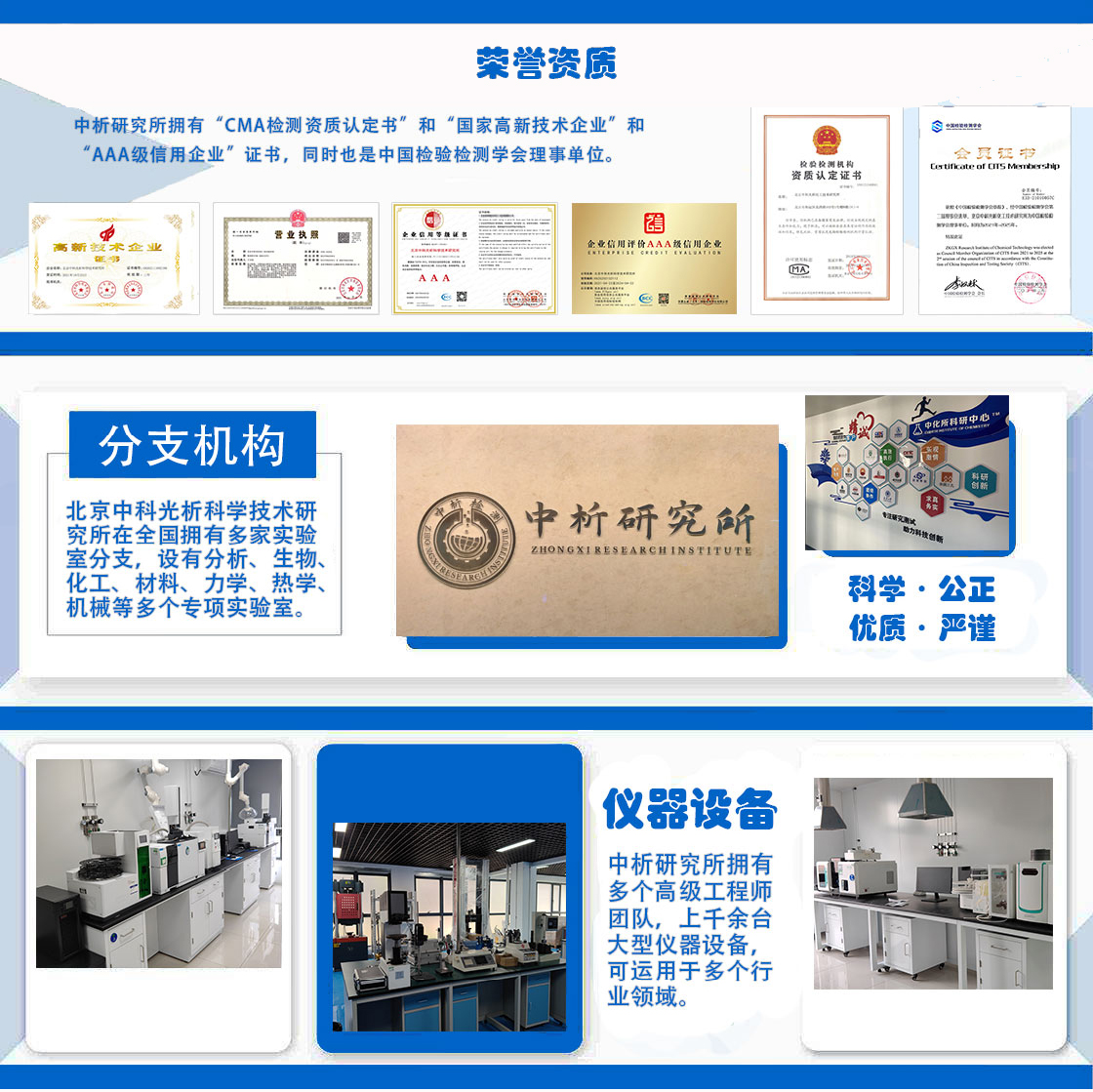
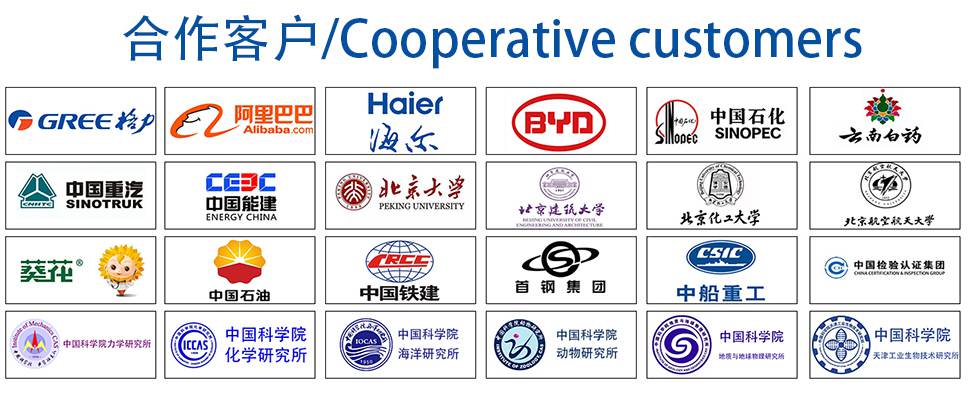