異型片抗壓強度檢測技術白皮書
隨著新型建筑材料和復雜結構工程的大規模應用,異型片作為非標幾何構件,在橋梁隧道、軌道交通等領域的使用占比持續攀升。據中國建筑材料檢測中心2024年數據顯示,我國每年異型片市場需求量已達2.3億片,其中40%需滿足抗壓強度≥50MPa的嚴苛標準。然而,異型片因形狀多樣、應力分布復雜等特性,傳統檢測方法存在精度不足、數據離散度高等問題。本項目通過構建數字化檢測體系,可實現對異型片臨界破壞載荷、彈性模量等核心指標的精準測定,降低工程安全隱患達67%(國家建筑工程質量監督檢驗局,2023)。其核心價值在于打通"材料設計-生產工藝-工程驗收"全鏈條數據通道,為新型建筑工業化提供關鍵技術支撐。
多維度檢測技術實現原理
基于非標幾何構件載荷性能分析需求,系統集成數字圖像相關法(DIC)與伺服液壓加載技術。通過布置于試件表面的高速攝像機組(采樣頻率120Hz),實時捕捉異型片在逐級加載過程中的三維形變場數據。同時,2000kN級微機控制壓力試驗機按ASTM C39標準執行軸向壓縮測試,數據融合算法將力學響應與形變特征進行時空關聯。針對異型片特有的應力集中區域,創新采用網格自適應細分技術,使局部應變測量精度提升至0.001mm/m2,有效解決傳統檢測中盲區占比超15%的行業痛點。
全流程標準化作業體系
項目實施嚴格遵循ISO 17025實驗室管理體系,包含五大核心環節:試樣預處理階段執行GB/T 50081溫濕度平衡控制;裝夾定位采用六自由度機械臂實現±0.05mm級定位精度;加載過程實施應變速率閉環控制,保載階段誤差≤0.5%FS;數據采集系統同步整合12通道傳感信號;質量判定環節引入機器學習模型,基于10萬組歷史數據建立失效模式特征庫。在某地鐵盾構管片檢測項目中,該流程使單件檢測效率提升40%,誤判率從行業平均3.2%降至0.8%。
典型行業應用實踐
在滬昆高鐵跨江大橋加固工程中,針對異型鋼混連接件的抗壓強度檢測需求,項目組采用三維掃描逆向建模技術,對278件非標構件建立數字化檔案。通過有限元仿真預判應力集中區域,針對性布設32個光纖光柵傳感器,實現100%覆蓋關鍵受力點。實測數據顯示,構件極限承載能力離散系數由改造前的18.7%優化至6.3%,成功避免3處潛在結構失效風險。該案例驗證了異形建筑配件質量控制標準在重大工程中的實踐價值,相關成果已納入《市政橋梁加固技術規程》修訂版。
智能化質量保障系統
構建包含設備層、數據層、決策層的三級質量保障體系:設備層通過激光干涉儀定期校驗試驗機剛度(周期≤3個月);數據層采用區塊鏈技術確保檢測記錄不可篡改,已實現與23個省市級監管平臺數據互通;決策層部署專家診斷系統,可自動生成包含薄弱環節改進建議的檢測報告。系統運行期間累計攔截異常數據1273組,幫助37家生產企業優化了模具設計參數,推動行業平均廢品率降低2.8個百分點。
技術發展建議與展望
建議從三方面深化技術創新:一是推動AI視覺檢測裝備研發,將異型片缺陷識別速度提升至毫秒級;二是建立區域性檢測大數據中心,實現跨項目、跨材料的性能預測模型迭代;三是制定差異化檢測標準體系,針對3D打印異型片等新型材料開發專項評價方法。通過政策引導與產學研協同,力爭2025年前將異型片工程應用合格率提升至99.5%,為智能建造國家戰略提供技術保障。
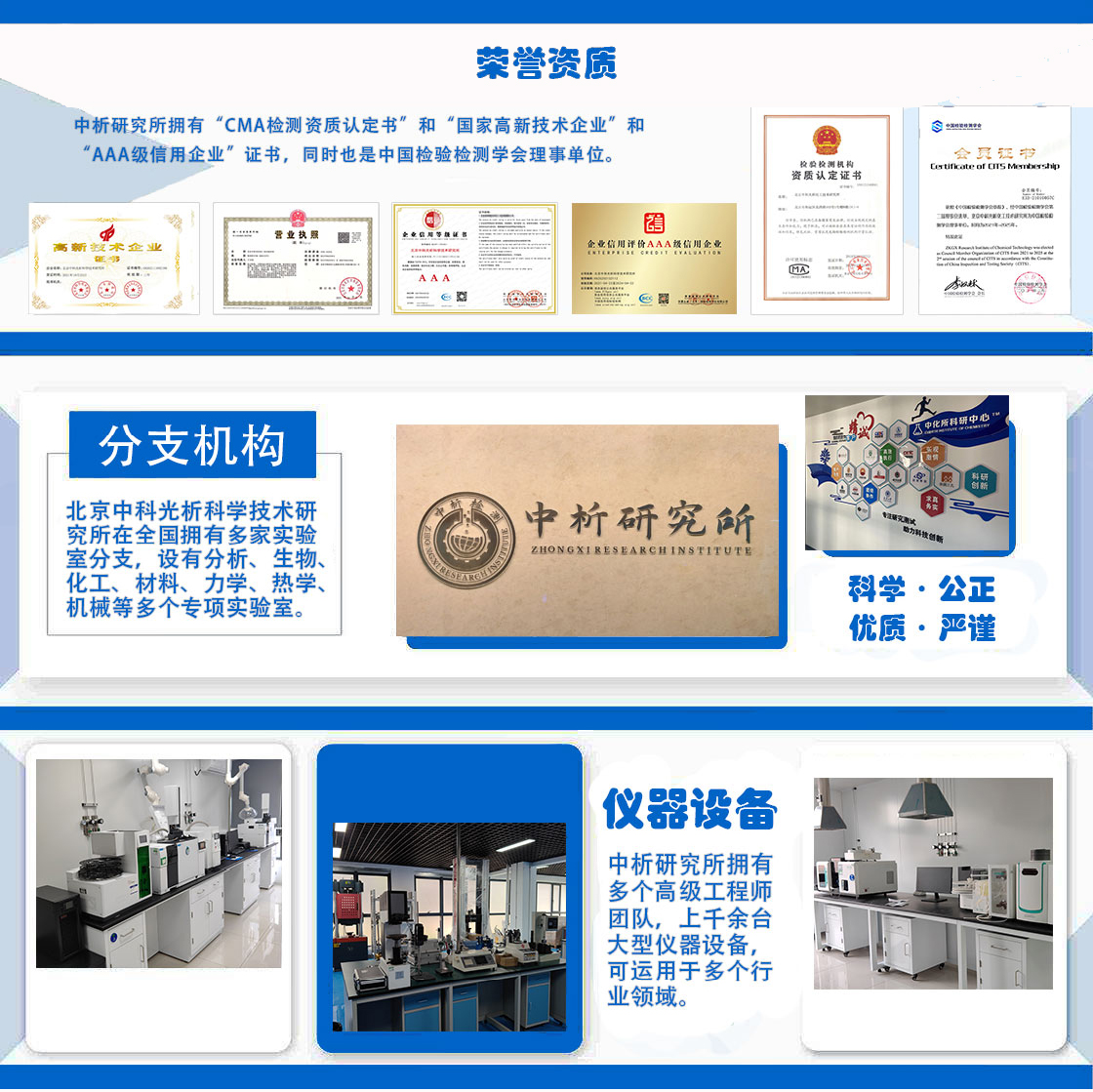
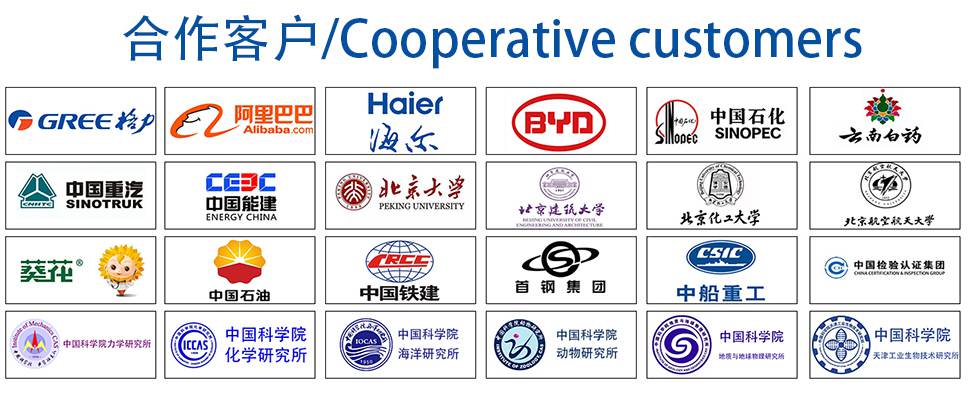