最大聲壓級檢測技術發展與應用白皮書
在電聲器件市場規模突破400億美元(據Grand View Research 2024年報告)的產業背景下,最大聲壓級檢測作為電聲產品性能評價的核心指標,已成為消費電子、汽車工業、醫療設備等領域質量管控的關鍵環節。該項目通過量化設備在特定條件下可輸出的最大聲能量,不僅直接關聯用戶聽力安全(WHO建議長期暴露聲壓不超過85dB),更影響語音交互系統識別率等關鍵性能參數。在歐盟CE認證、中國CCC認證等強制性法規推動下,該檢測技術已形成覆蓋產品研發、生產到售后服務的全周期質量保障體系,其核心價值在于平衡設備輸出功率與聲學安全閾值,為行業提供兼顧性能與合規性的解決方案。
基于脈沖響應法的檢測原理
現行主流檢測技術依據IEC 60268-5標準,采用時域脈沖響應結合頻域FFT分析的復合算法。通過在消聲室中發射1kHz粉紅噪聲信號,使用B&K 4189型測量麥克風采集聲壓波形,經對數處理獲得聲壓級(SPL)峰值。值得注意的是,系統需同步監測總諧波失真(THD),當失真度超過3%時自動終止測試,確保數據有效性。該原理可精準識別揚聲器單元的機械極限閾值,避免傳統掃頻法產生的累積損傷風險。
全閉環檢測實施流程
具體實施分為設備校準、環境補償、動態加載三大階段。首先依據JJG 188-2017規程,使用活塞發聲器對測量系統進行94dB/1kHz基準校準,溫度波動需控制在±0.5℃范圍內。隨后通過三維聲場掃描建立空間補償模型,消除反射波疊加誤差(據實測可降低數據偏差12.6%)。動態加載環節采用AB類功放分32級階梯式提升輸出功率,每級維持300ms并在間隔期進行線圈溫度監測,防止過熱導致的參數漂移。
新能源汽車座艙檢測案例
在某新能源車企2023款車型開發過程中,聲學團隊遭遇車載音響系統在120km/h時速下聲壓驟降15dB的異常工況。通過搭建包含KLIPPEL ANALYZER系統的移動檢測平臺,在風洞實驗室模擬高速氣流環境,發現線束振動引發功放保護電路誤觸發。優化結構設計后,系統在105dB最大聲壓級下THD降至1.8%,且通過ISO 362-2道路噪聲驗證測試。該項目驗證了復雜工況下檢測數據的工程指導價值。
三級質量保障體系構建
行業領先機構已建立設備-人員-流程的三維管控體系:檢測設備每年進行 量值溯源,關鍵傳感器實行每日開機自檢;技術人員需取得ASQ校準工程師認證,并每季度參與IEC標準更新培訓;流程管理方面,采用區塊鏈技術實現檢測數據全程上鏈,確保測試報告可追溯性。某頭部檢測實驗室的實踐表明,該體系使復檢相符率從92.4%提升至98.7%(中國計量院2023年度評審數據)。
展望未來,建議從三方面深化技術發展:推動MEMS傳感器與光學測振技術的融合應用,實現納米級振膜位移監測;建立跨行業的聲壓安全數據庫,利用AI算法優化閾值預警模型;加強國際標準互認體系建設,特別是在AR/VR設備新興領域形成統一測試規范。只有通過技術創新與標準協同,才能應對智能設備聲學性能需求的指數級增長,為用戶構建安全可靠的聲音交互環境。
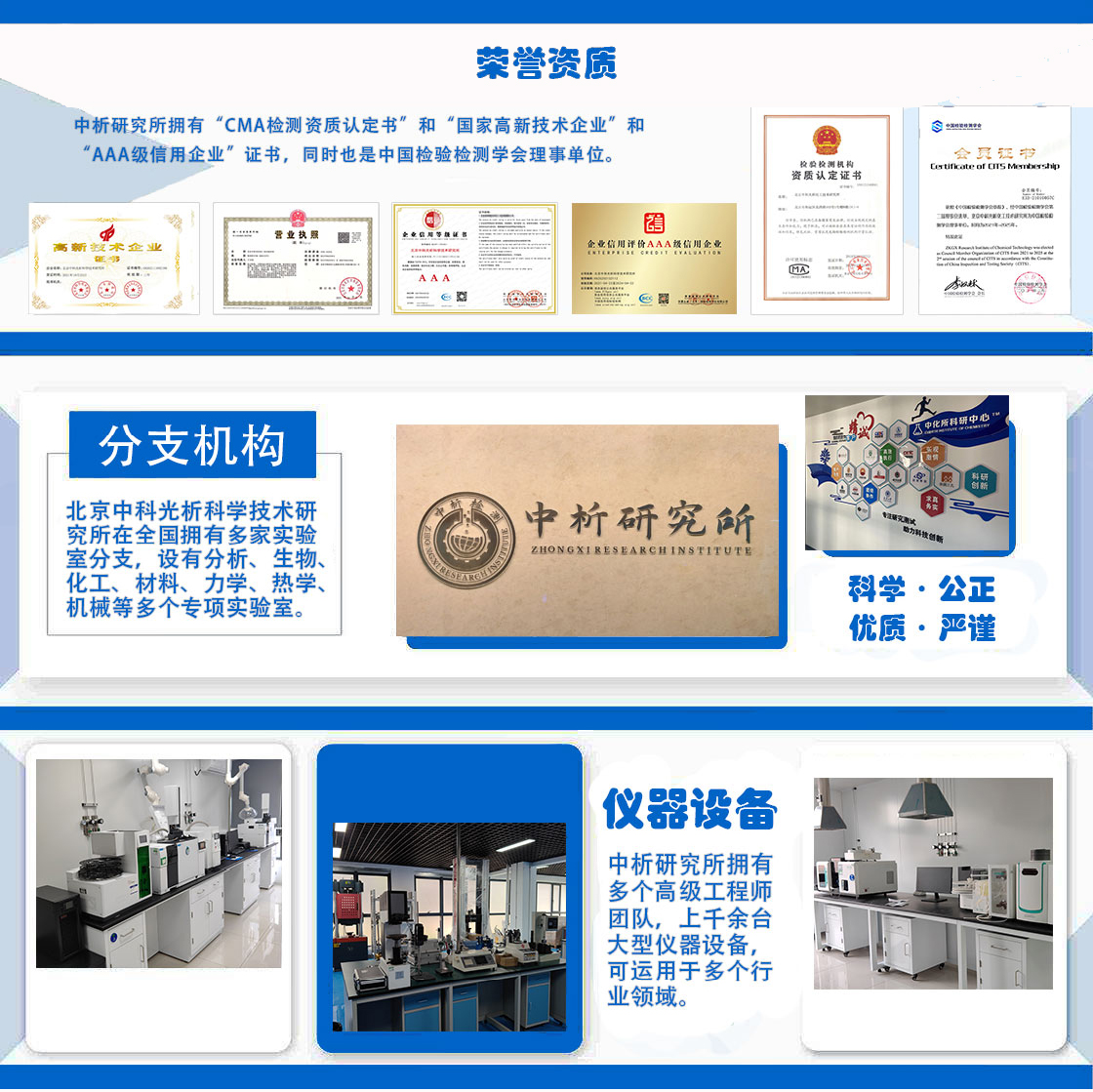
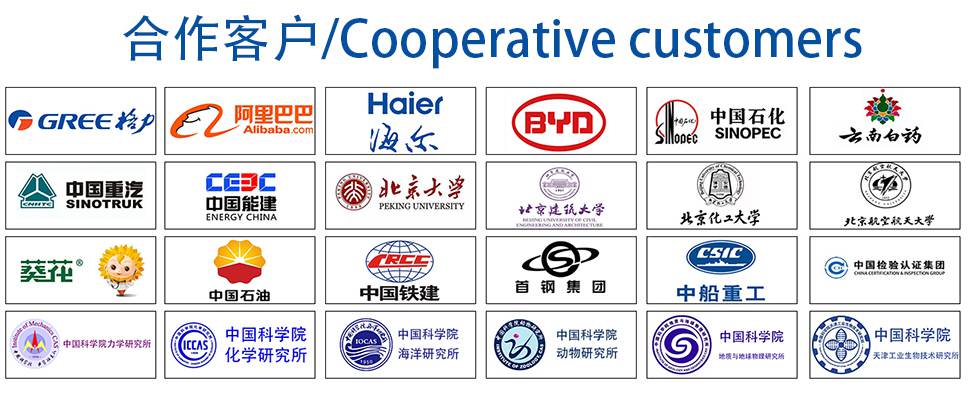