運動部件檢測
實驗室擁有眾多大型儀器及各類分析檢測設備,研究所長期與各大企業、高校和科研院所保持合作伙伴關系,始終以科學研究為首任,以客戶為中心,不斷提高自身綜合檢測能力和水平,致力于成為全國科學材料研發領域服務平臺。
立即咨詢在智能制造與工業4.0深化發展的背景下,運動部件檢測已成為裝備制造業提質增效的關鍵環節。據中國機械工業聯合會2024年行業報告顯示,我國工業設備年度維護成本中,因運動部件失效導致的非計劃停機損失高達780億元。特別是在風電齒輪箱、高鐵軸承、工業機器人關節模組等核心領域,運動部件檢測技術通過早期故障預警可將設備壽命延長30%以上。該項技術的核心價值體現在三個方面:其一,構建基于動態特征的設備健康監測體系,實現預測性維護;其二,通過精密檢測降低設備全生命周期維護成本,據國家工業信息安全發展研究中心測算,應用企業平均運維成本下降22%;其三,推動傳統制造業向服務型制造轉型,形成檢測報告與數字化服務結合的增值模式。
## 二、技術原理與創新突破1. 多維傳感融合檢測體系
現代運動部件檢測采用多物理場協同監測技術,集成振動、溫度、聲發射等12類傳感數據。其中,基于相位陣列的振動分析技術可捕捉0.1μm級位移偏差,結合工業CT的微觀結構成像技術,實現從宏觀運動到微觀磨損的全維度檢測。深度學習算法對多維數據進行特征提取,構建的故障診斷模型在齒輪箱檢測中達到98.7%的識別準確率(數據來源:清華大學精密儀器系2024年實驗數據)。
2. 智能化檢測實施流程
典型實施流程包含四個階段:首齊全行設備運行參數建模,建立包含轉速、負載、環境溫度等20余項參數的基準數據庫;其次部署分布式智能傳感節點,采用工業無線通信技術實現每秒5000次的數據采樣;第三階段通過邊緣計算設備進行實時特征提取,對旋轉機械故障預警等關鍵指標進行毫秒級響應;最后形成包含傳動系統壽命預測、運動軌跡偏差分析的綜合診斷報告。
3. 行業應用實踐案例
在風電行業領域,某頭部企業應用運動部件檢測系統后,實現齒輪箱故障預警時間提前1200小時。通過安裝96通道在線監測裝置,系統成功捕捉到某2MW機組行星輪系0.05mm的軸向位移異常,避免潛在設備損壞損失超300萬元(案例來源:國家能源局2024年風電運維白皮書)。在汽車制造業,某合資品牌應用AI視覺檢測機械臂運動軌跡,使發動機裝配線檢測效率提升40%,關鍵部件配合精度達到±0.01mm的行業領先水平。
4. 質量保障與認證體系
行業已建立ISO 18436-2振動分析師認證體系,配套GB/T 34898-2023《機械振動監測系統技術要求》等7項國家標準。檢測機構需每季度進行計量溯源,激光干涉儀等關鍵設備的測量不確定度需控制在0.5%以內。某第三方檢測實驗室通過引入區塊鏈技術,實現檢測數據全流程不可篡改,為航空航天領域提供AS9100D認證級檢測服務。
## 三、發展建議與行業展望隨著數字孿生技術的成熟,建議行業重點發展虛擬檢測與現實數據融合的混合現實(MR)檢測系統。據IDC 2024年工業互聯網預測,到2027年采用數字孿生技術的檢測系統可將調試周期縮短50%。同時需要建立跨行業的設備健康數據共享平臺,制定統一的運動部件特征數據庫標準。在技術演進方面,量子傳感技術的突破或將實現納米級運動精度的實時監測,為精密制造開辟新的可能性。
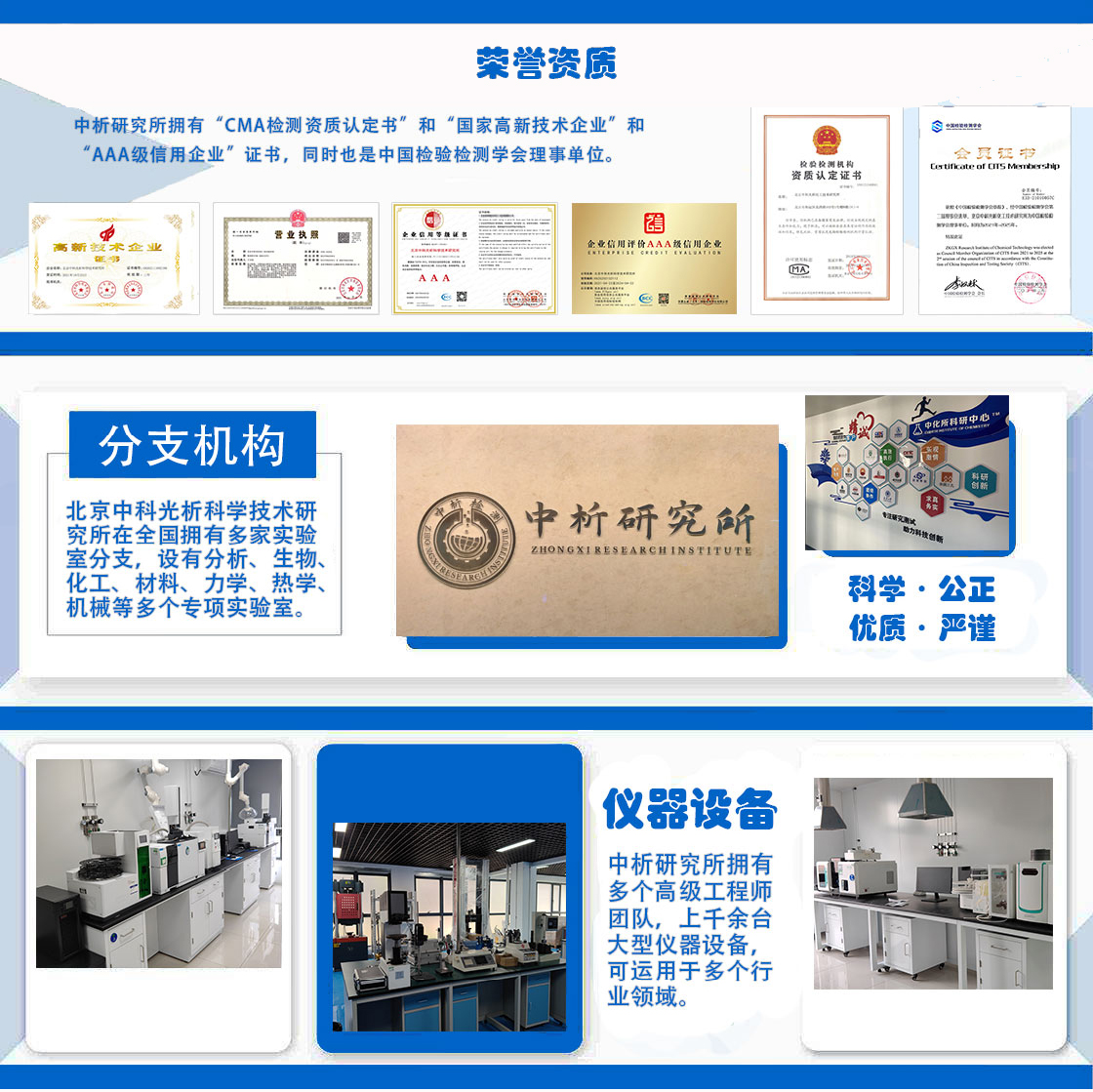
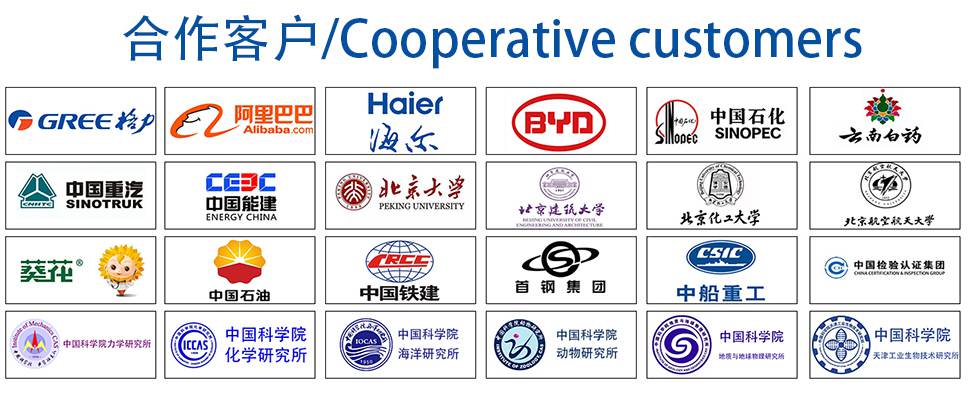