殼體鈑金成型設備檢測
殼體鈑金成型設備是工業生產中用于加工金屬板材的關鍵設備,廣泛應用于汽車制造、航空航天、電子設備外殼等領域。這類設備通過沖壓、彎曲、拉伸等工藝,將平板金屬成型為復雜的三維殼體結構,如車身外殼、機箱或容器。檢測在整體生產流程中扮演著至關重要的角色,它不僅直接影響產品質量和性能,還關乎設備的安全運行和使用壽命。質量不合格的殼體可能導致結構強度不足、裝配困難或安全隱患,進而引發客戶投訴、成本損失甚至安全事故。因此,定期對殼體鈑金成型設備進行系統化檢測,能有效預防潛在缺陷,確保設備輸出符合設計規范和行業要求的精密零件。檢測過程通常涉及多個維度,從初始的設備校準到最終的產品驗證,需要綜合考慮設備自身的機械狀態、加工精度以及成品的一致性和可靠性。在現代智能制造背景下,檢測技術的創新如數字化和自動化整合,正推動檢測效率的提升,幫助企業在競爭激烈的市場中保持優勢。
檢測項目
殼體鈑金成型設備的檢測項目涵蓋了設備性能、加工過程及成品質量多個方面。首先,設備性能檢測包括運動精度(如滑塊行程和平行度)、動力系統狀態(如液壓或氣壓穩定性)和結構完整性(如框架變形或部件磨損)。這些項目確保設備自身運行可靠,避免因機械故障導致加工偏差。其次,加工過程檢測聚焦于成型精度,例如檢查沖壓模具的對中性、彎曲角度的一致性和拉伸力的均勻性,以防止材料撕裂或起皺。最后,成品質量檢測是核心,涉及殼體零件的尺寸精度(如長寬高公差)、幾何形狀(如圓度或平面度)、表面質量(無劃痕、凹陷或氧化)和力學性能(如硬度或抗拉強度)。常見的具體項目包括:尺寸偏差控制在±0.1mm內、表面粗糙度Ra值低于1.6μm,以及無裂紋或氣泡缺陷。這些項目需定期執行,以確保設備輸出一致的高品質產品。
檢測儀器
在殼體鈑金成型設備檢測中,使用專業儀器高效收集數據,確保檢測的準確性和可重復性。基礎儀器包括千分尺和游標卡尺,用于手動測量尺寸精度和厚度偏差;它們操作簡單但適用于小批量檢測。對于高精度要求,三坐標測量機(CMM)是核心設備,能通過激光或探針掃描三維幾何形狀,自動分析圓度、平面度等參數,精度可達0.001mm。表面質量檢測常用表面粗糙度儀和光學顯微鏡,前者量化Ra值,后者放大觀察微缺陷如劃痕或蝕坑。力學性能測試則依賴硬度計(如洛氏硬度計)和萬能材料試驗機,用于評估殼體材料的硬度和抗拉強度。此外,自動化系統如激光掃描儀和工業相機集成到生產線中,實現實時在線檢測,提高效率。這些儀器需定期校準,確保符合國家計量標準(如JJG規程),以避免誤差累積。
檢測方法
殼體鈑金成型設備的檢測方法多樣,結合手動和自動技術以適應不同場景。首先,手動檢測法包括視覺檢查(用放大鏡或裸眼觀察表面缺陷)和觸覺測量(如使用卡尺或塞規驗證尺寸),適用于快速抽查或初步評估;但依賴操作者經驗,易引入主觀誤差。其次,半自動方法如使用三坐標測量機進行編程掃描,通過軟件生成3D模型對比CAD設計,能精確分析幾何偏差,適合批量檢測。破壞性測試法涉及取樣進行力學實驗,例如拉伸測試以確定材料極限強度,或彎曲測試評估韌性;但會破壞樣品,僅用于抽樣驗證。非破壞性方法更常用,如超聲波探傷檢測內部裂紋或X射線成像分析焊縫質量。自動化檢測系統集成傳感器和AI算法,實現設備運行狀態的實時監控和預測維護。所有方法需遵循標準化流程,包括預處理(清潔樣品)、數據采集和結果分析,確保重復性和可靠性。
檢測標準
殼體鈑金成型設備檢測嚴格遵循國內外標準,以保證檢測結果的權威性和可比性。國際標準如ISO 9001質量管理體系,要求建立檢測程序和控制計劃;ISO 2768-1和ISO 2768-2規范了尺寸和幾何公差,適用于殼體零件的精度評估。中國國家標準(GB/T)是核心依據,例如GB/T 1804規定了一般公差等級,GB/T 4340.1關于維氏硬度測試方法,以及GB/T 228.1對材料拉伸性能的測試要求。行業專用標準如汽車領域的QC/T 490(汽車車身制造檢測規范),強調表面光潔度和強度指標。設備檢測還需遵守機械安全標準如GB/T 15706,確保操作防護和風險控制。這些標準不僅規定了檢測限值(如尺寸公差±0.2mm),還涉及儀器校準(依據JJF 1033)和報告格式(需記錄檢測數據、時間和負責人),促進貿易和質量一致性。定期更新標準以融入新技術(如數字化檢測),是提升檢測水平的關鍵。
綜上所述,殼體鈑金成型設備檢測是一個系統化工程,通過綜合檢測項目、儀器、方法和標準,能有效提升設備可靠性和產品質量。隨著工業4.0發展,智能檢測技術如AI和物聯網的應用,將推動檢測向高效、精準方向演進,為企業帶來更大價值。
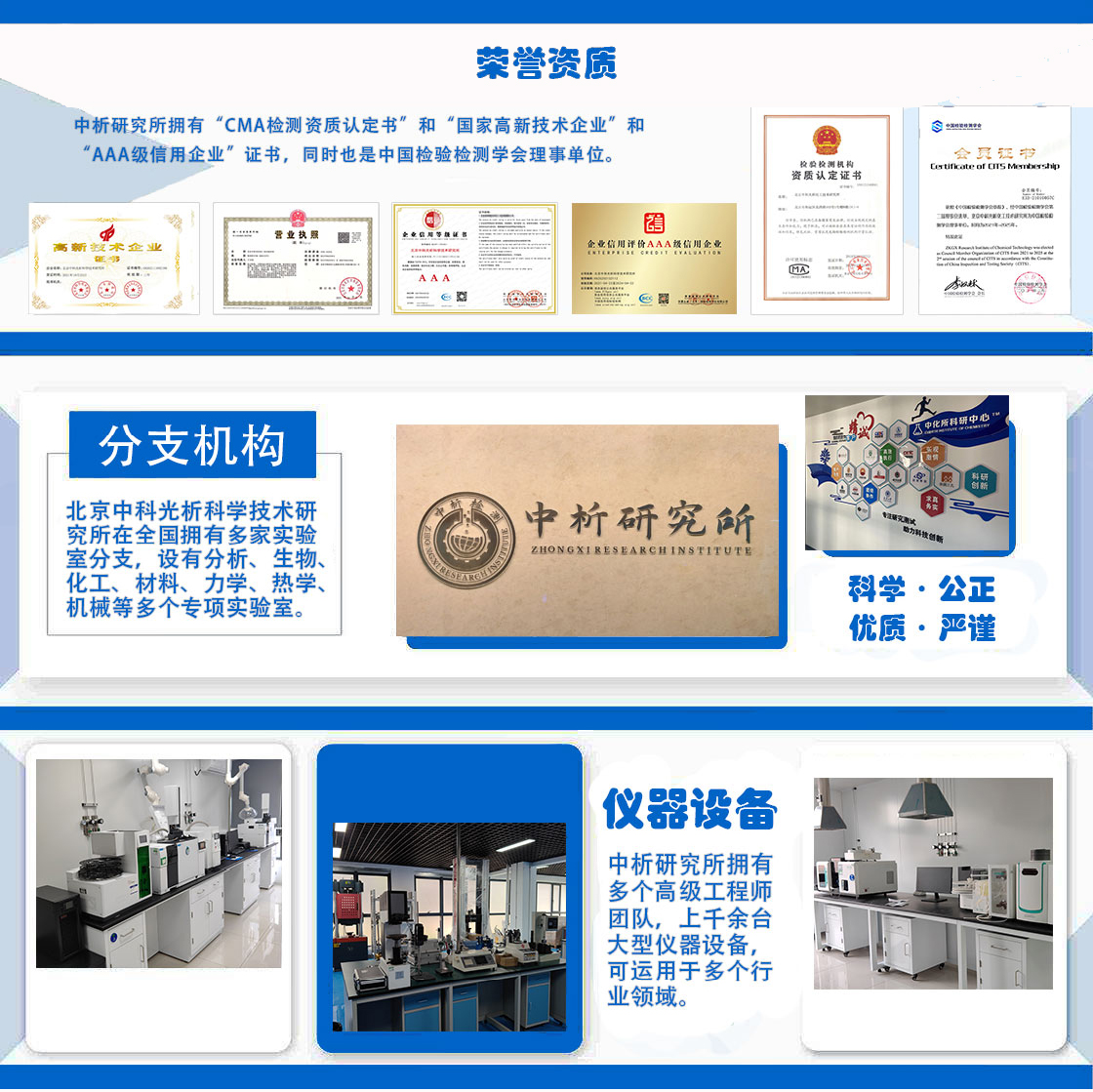
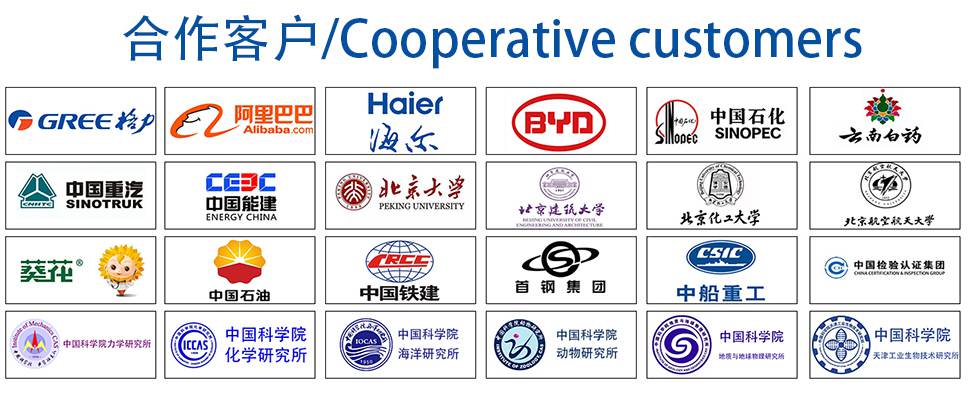