承壓設備產品焊接試件檢測概述
承壓設備產品焊接試件檢測是壓力容器、鍋爐、管道等承壓設備制造過程中的核心質量控制環節。焊接試件是從設備本體或專門制作的樣品中提取的焊縫樣本,用于全面評估焊接質量、確保設備在高壓、高溫或腐蝕性環境下能夠安全穩定運行。這種檢測至關重要,因為焊接缺陷如裂紋、氣孔或未熔合可能導致設備失效,引發安全事故、環境污染或經濟損失。在石油化工、能源、造船等工業領域,焊接試件檢測不僅是法規要求(如中國《特種設備安全法》),也是產品認證(如ASME認證)的基礎。檢測過程通常包括非破壞性和破壞性測試,旨在驗證焊縫的完整性、力學性能和微觀結構。通過系統化的檢測,制造商能優化焊接工藝,提升設備壽命,并符合國際和國內安全規范。
檢測項目
承壓設備產品焊接試件的檢測項目旨在覆蓋焊縫的全面性能評估,確保無缺陷并滿足設計規范。主要項目包括:
- **外觀檢查**:通過目視或放大鏡觀察焊縫表面,檢測裂紋、咬邊、氣孔、夾渣等可見缺陷,這是初步質量篩選的關鍵步驟。
- **無損檢測(NDT)**:包括射線檢測(RT)用于內部缺陷識別,超聲波檢測(UT)針對厚度方向缺陷,磁粉檢測(MT)或滲透檢測(PT)用于表面裂紋檢測。
- **力學性能測試**:涉及拉伸試驗評估抗拉強度和屈服強度,彎曲試驗檢驗延展性和抗裂紋能力,以及沖擊試驗測定韌性(如夏比V型缺口試驗)。
- **化學成分分析**:通過光譜儀等手段,驗證焊縫金屬的成分是否符合材料標準,控制元素(如碳、硫)含量以防止腐蝕或脆化。
- **金相檢驗**:使用顯微鏡觀察焊縫微觀結構,檢查晶粒大小、熱影響區變化及潛在缺陷(如未熔合或氧化夾雜)。這些項目綜合起來,確保試件從宏觀到微觀均達到安全閾值。
檢測儀器
承壓設備焊接試件檢測依托專業儀器實現高精度測量,確保數據的可靠性和可重復性。常用儀器包括:
- **射線檢測儀**:如X射線機或γ射線源,配合數字探測器或膠片,用于生成焊縫內部缺陷的圖像(例如蔡司Xradia系統)。
- **超聲波探傷儀**:便攜式或固定設備(如奧林巴斯EPOCH系列),發射高頻聲波通過探頭接收回波,分析內部缺陷的位置和大小。
- **力學測試設備**:萬能材料試驗機(如Instron 5982)進行拉伸、彎曲和壓縮測試,沖擊試驗機(如Tinius Olsen)測量沖擊韌性,硬度計(如布氏或洛氏硬度計)評估表面硬度。
- **化學成分分析儀**:直讀光譜儀(如ARL 3460)或X射線熒光光譜儀,快速分析金屬元素的組成。
- **金相顯微鏡**:光學或電子顯微鏡(如蔡司Axio Scope),用于微觀結構觀察和缺陷分析,常配備圖像分析軟件。這些儀器需定期校準(依據ISO 17025標準),以保證檢測精度和一致性。
檢測方法
承壓設備焊接試件檢測方法基于科學流程和標準化操作,確保結果的可比性和有效性。主要方法包括:
- **射線檢測方法**:制備試件后,使用X射線或γ射線照射,通過膠片成像或數字探測器捕獲圖像;缺陷分析依據灰度對比和尺寸測量,常用曝光參數如電壓和電流需優化以覆蓋不同厚度。
- **超聲波檢測方法**:清潔試件表面,耦合劑涂抹后,探頭沿焊縫移動;發射超聲波脈沖,接收回波信號,通過A-scan或B-scan顯示分析缺陷深度和位置;方法強調角度調整和校準塊使用以提高分辨率。
- **力學性能測試方法**:拉伸試驗中,將標準試樣夾持在試驗機上,施加軸向載荷直至斷裂,記錄應力-應變曲線;彎曲試驗采用三點彎曲或四點彎曲,評估裂紋擴展;沖擊試驗則在低溫下進行,測量能量吸收值。
- **金相檢驗方法**:切割試件,研磨拋光至鏡面,蝕刻(如用硝酸酒精溶液)后顯微鏡觀察;圖像分析軟件量化晶粒尺寸和缺陷百分比。所有方法需遵循標準操作規程,確保人員資質(如II級或III級NDT證書)和環境控制。
檢測標準
承壓設備焊接試件檢測嚴格遵守國際和國內標準,保證兼容性和安全性。主要標準包括:
- **國際標準**:ASME Boiler and Pressure Vessel Code(ASME BPVC Section IX)規定焊接工藝評定和試件測試要求;ISO 5817《焊接質量等級》定義缺陷接受準則;EN ISO 15614系列覆蓋力學試驗方法。
- **國內標準**:GB/T 150-2011《壓力容器》全面規范試件檢測流程;GB/T 3323-2005《金屬熔化焊焊接接頭射線照相》詳述射線檢測技術;GB/T 2650-2008《焊接接頭沖擊試驗方法》指導沖擊測試。
- **行業特定標準**:如API 510《壓力容器檢驗規范》用于石油行業,或TSG 21-2016《固定式壓力容器安全技術監察規程》在中國強制執行。這些標準明確定義了檢測參數、接受標準(如允許缺陷尺寸)和報告格式,確保檢測結果具有法律效力和互認性。制造商必須依據這些標準進行第三方認證,以獲取市場準入。
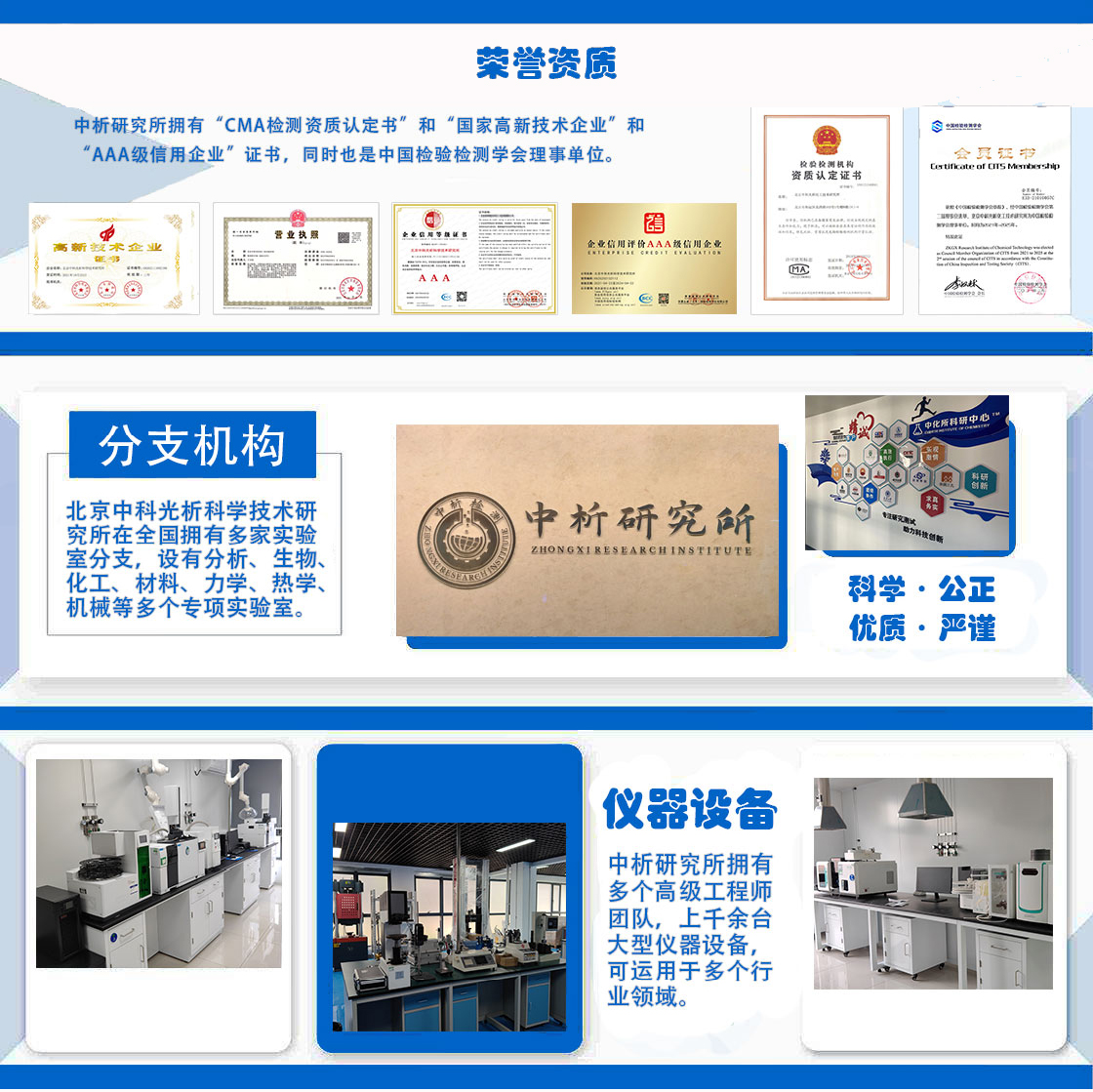
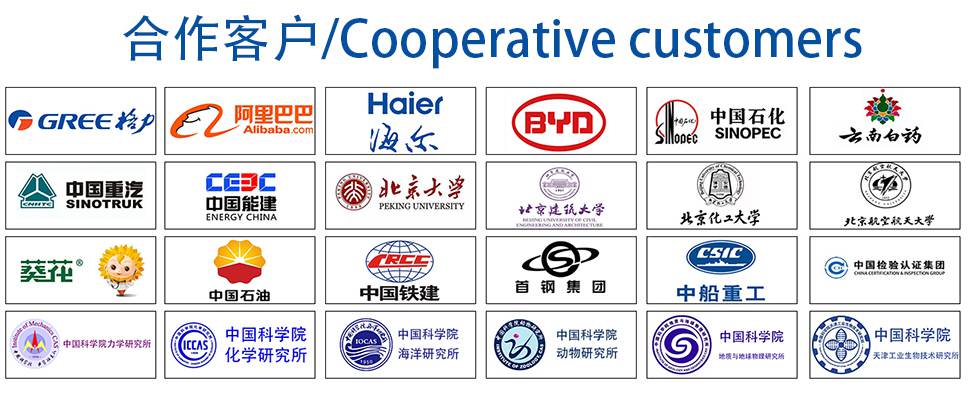