飛機航空機輪和剎車裝置連續剎車試驗檢測
飛機航空機輪和剎車裝置連續剎車試驗檢測
飛機作為現代交通工具的核心組成部分,其安全性能直接關系到人員和貨物的生命財產安全。在飛機的各個系統中,機輪與剎車裝置是保證飛機地面運行安全的重要部件。特別是在起降階段,剎車裝置在飛機減速和停止中的表現尤為關鍵。因此,開展飛機航空機輪和剎車裝置的連續剎車試驗檢測,不僅是評估其性能和可靠性的必備環節,也是航空安全領域的重要保障。
連續剎車試驗檢測的背景與意義
在飛機著陸過程中,尤其在跑道有限或緊急情況下,剎車裝置的性能決定了飛機是否能安全而迅速地停止。剎車裝置的設計需保證在高溫、高摩擦和高頻使用條件下,依然具備穩定的剎車能力和使用壽命。然而,在實際運行中,剎車裝置經常面臨高強度、連續工作的挑戰。例如,連續滑行、大量短途起降航班的運行,都會導致剎車部件的負荷增加。因此,對剎車裝置進行連續剎車試驗檢測,不僅能夠測試其在極端條件下的表現,還能判斷部件的疲勞壽命、耐高溫性能以及工作表現,這對保障飛行安全至關重要。
連續剎車試驗檢測的實施流程
連續剎車試驗檢測需要嚴格按照航空工業標準實施,測試過程通常分為以下幾個主要步驟:
1. 環境與設備準備
試驗需在模擬真實機場環境的試驗場地中進行,確保機輪和剎車裝置在條件上接近實際使用情況。用于測試的設備需要包括高精度的剎車力檢測儀器、溫度監控系統、數據記錄儀,以及其他相關加載裝置。此外,測試的剎車裝置需經過嚴格的安裝和調試,確保其狀態在初始階段是最優的。
2. 連續剎車模擬
試驗通過模擬飛機從高空滑行降落,機輪接觸地面后逐漸減速至停止的過程進行。通常會設置多個連續剎車操作,以模擬真實機場起降運行中可能的高頻剎車任務。例如:以固定間隔重復進行10次或更多次急剎,或按照起飛-剎車-滑停的模式反復循環。在這一過程中,剎車溫度、剎車壓力、制動力矩等關鍵參數都會被實時監控與記錄。
3. 高溫條件下性能檢測
連續剎車會導致剎車裝置尤其是制動盤和制動片產生高溫,這會影響剎車材料的物理特性和工作表現。檢測內容需包括在高溫條件下的制動力變化、剎車響應速度,以及是否出現熱衰減、材料失效等問題。這項試驗旨在驗證剎車裝置的熱穩定性和耐久性。
4. 磨損與疲勞分析
剎車裝置在多次高強度操作過程中,其制動材料會不可避免地出現磨損現象。通過檢測制動盤與制動片在試驗結束后的磨耗量,以及基于微觀分析尋找裂紋或材料疲勞的跡象,可以評估剎車裝置的使用壽命和維修需求。
5. 數據整理與分析
整個試驗結束后,大量的實驗數據需要進行系統化整理與分析。包括制動力隨時間的曲線變化、剎車溫度分布、磨損率,以及剎車測試中記錄到的異常現象。這些數據為剎車裝置性能的定量評估提供了重要依據。
連續剎車試驗中可能遇到的技術難點
在進行剎車裝置的連續剎車試驗中,可能面臨以下幾個主要技術難點:
1. 高溫效應處理
連續剎車會引發極高的溫升,在高溫狀態下,剎車制動材料可能因熱衰減導致性能下降,甚至可能出現熱裂紋等問題。如何準確模擬真實剎車場景下的高溫效應,并對其進行有效測量和評估,是一個關鍵挑戰。
2. 數據的高精度采集與處理
多個傳感器需在高動態環境下同步工作,實時采集精確的數據。然而,在測試過程中高溫、高振動、復雜力學作用等因素可能會引入噪聲,威脅數據的準確性。因此,如何排除測量干擾,并對大量數據進行高效處理和分析,也是工程實現中的重要難點。
3. 材料性能的評估復雜性
剎車裝置的材料需具備高摩擦系數、耐高溫、抗疲勞的特性,而不同材料在相同環境條件下的表現可能存在顯著差異。材料的磨損特性與疲勞表現還會受到環境溫度、濕度等因素的影響,這對剎車裝置的性能分析提出了更高的要求。
連續剎車試驗檢測的應用與未來發展
目前,航空機輪與剎車裝置的連續剎車試驗檢測已成為航空工業研發和質量管理的重要環節之一。試驗結果不僅為新產品的設計改良提供數據支持,還為了解評估現役飛機剎車系統的狀態提供了科學依據。
未來,隨著航空技術的進步和飛機運行環境的變化,連續剎車試驗檢測也在不斷發展。例如,在檢測設備方面,借助物聯網和人工智能技術,可實現更加高效的數據采集與智能化分析;在剎車裝置設計方面,輕量化材料和復合材料的引入將進一步優化裝置性能。在實際運行中,運用數字孿生技術,將試驗數據與真實使用情況結合,可以創建更為精確的剎車裝置性能模型,從而為航空安全提供更加全面的保障。
總結
飛機航空機輪和剎車裝置的連續剎車試驗檢測不僅是對產品性能的嚴格考驗,也是對飛行安全的負責。這一過程確保了剎車裝置在各種復雜條件下均能保持穩定可靠的工作表現。從檢測流程到技術難點,再到未來發展方向,試驗檢測體系的完善不僅反映了航空工業技術水平的進步,更為航空事業的安全運行提供了堅實支撐。
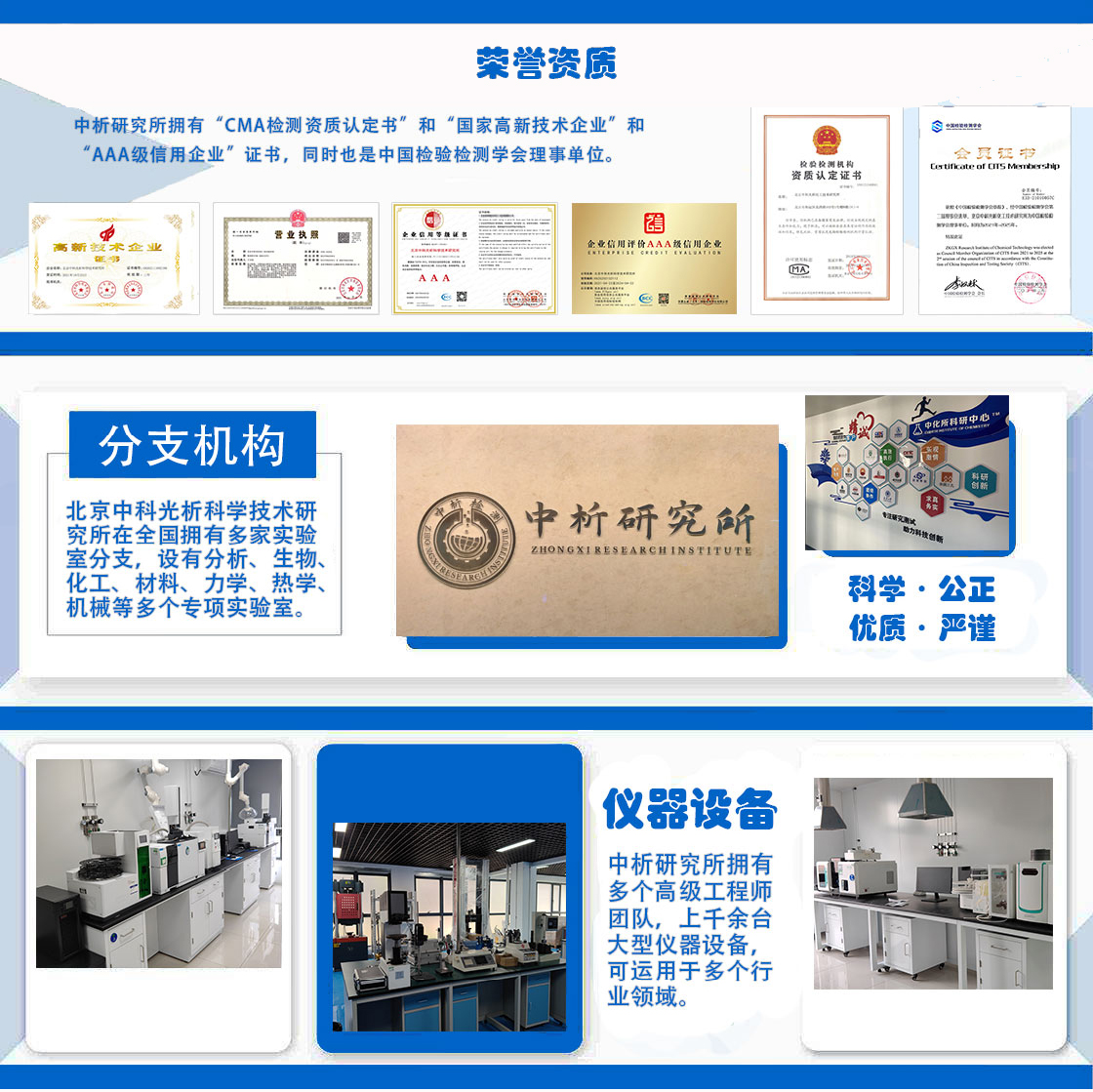
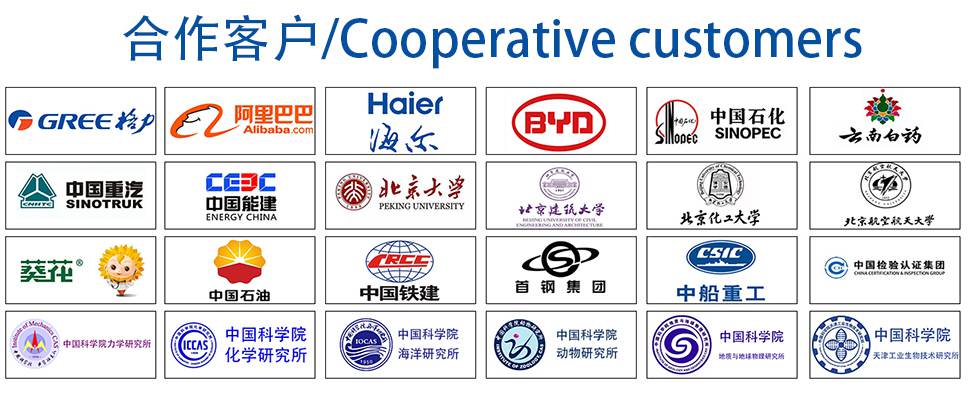