飛機航空機輪和剎車裝置剎車裝置粘結程度試驗檢測
# 飛機航空機輪和剎車裝置剎車裝置粘結程度試驗檢測
飛機的航空機輪和剎車裝置是確保飛行器在地面運行和安全??康年P鍵部件,其中剎車裝置的性能尤為重要。在剎車裝置的性能檢測中,粘結程度試驗是一個不可或缺的重要環節。通過這種檢測,可以評估剎車片與剎車盤之間的結合狀況,從而確保剎車系統的可靠性和耐用性。以下內容將圍繞航空機輪和剎車裝置的結構特點、粘結程度試驗的意義、試驗方法及其結果分析等方面展開論述。
## 航空機輪和剎車裝置的結構與功能
航空機輪是飛機在地面運行時的基礎支撐結構,而剎車裝置則為飛機著陸減速和地面停留提供必要的制動力。一般來說,航空機輪和剎車裝置主要包括輪轂、輪胎、剎車盤、剎車片,以及驅動力的傳遞機構。
剎車系統通過將動能轉化為熱能的方式達到減速甚至停機的目的。當飛機著陸時,剎車裝置需要承受巨大的沖擊力和高溫環境,因此其材料和制造工藝必須具有極高的強度和耐熱性。而剎車片與剎車盤表面的良好粘結,是傳遞剎車壓力并實現可靠制動性能的關鍵環節。
正常運行的剎車系統可以在緊急情況下有效地減速,從而避免事故。然而,如果剎車片與剎車盤的粘結不牢固,可能導致剎車失效,影響飛行安全。因此,科學地評估剎車裝置粘結程度具有重要意義。
## 剎車裝置粘結程度試驗的意義
剎車裝置粘結程度試驗是為了評估剎車片和剎車盤表面在實際工作條件下的連接質量。試驗的主要目的是確保兩者在高壓、高溫及長期使用環境下仍能保持緊密結合,從而避免因粘結失效引發的滑移或分離。
在飛機運行過程中,著陸時的高強度制動會使剎車盤表面出現高溫和劇烈摩擦。這些劇烈的工作條件考驗著剎車裝置的耐用性,尤其是粘結性能。如果剎車片產生移位或剝離,不僅會導致制動力嚴重不足,還可能對周圍機械零件造成劇烈破壞。
因此,通過粘結程度試驗,技術人員能夠識別潛在的問題,并在生產和維修過程中對剎車裝置采取有效的改進措施。這種檢測相對于事后修復,更有助于從根本上提高飛行器的安全水平。
## 粘結程度試驗的基本方法
剎車裝置的粘結程度試驗主要通過多種工藝和測試條件展開,其常用的試驗方法包括靜態測試、動態測試和環境模擬試驗等。以下逐一介紹具體的操作流程和技術要點。
### 1. 靜態加載試驗
靜態加載試驗是最基本的粘結性能檢測方法。試驗時,將剎車片和剎車盤組裝成一個完整的制動系統后,利用試驗臺對剎車片施加恒定的靜壓力,觀察其與剎車盤的粘結狀態。
這一試驗主要用于驗證剎車片材料的粘結強度以及涂膠工藝的質量。一旦觀察到剎車片與剎車盤出現剝離、裂紋或粘結不均的現象,則意味著檢測未通過,需進一步分析原因并調節生產工藝。
### 2. 動態摩擦試驗
動態摩擦試驗模擬的是飛機高速著陸時剎車裝置實際運行的狀態。這一試驗通常借助高轉速的剎車試驗機來完成,通過將剎車盤加速至指定轉速并施加剎車片的方式,測試其在高溫條件下的粘結穩定性。
試驗過程中需密切測量剎車片與剎車盤之間的接觸狀態、表面溫度分布以及制動力衰減曲線。如果粘結不良,則容易在摩擦過程中出現剝離或大幅度溫度突變,這是不合格的標志。
### 3. 環境模擬試驗
由于飛機需在復雜多變的氣候條件下運行,剎車裝置粘結性能還需接受環境因素的影響測試。試驗模擬高濕度、低溫、高溫及極端晝夜溫差等條件,檢測剎車片與剎車盤是否出現粘結質量下降的現象。
具體測試方法包括將剎車裝置置于高低溫濕熱箱內進行老化試驗或通過試驗設備模擬降雨、積雪工況,用以評估材料的耐候性和耐用性。
## 檢測結果與分析
通過上述試驗方法得到的檢測數據可以反映出剎車裝置的整體粘結質量。以下是試驗結果的幾種可能情況及對應的分析:
### 1. 粘結性能良好
如果剎車裝置在所有試驗環境條件下均未出現剝離、滑移,且其制動力輸出穩定,則說明剎車片與剎車盤達到了出色的粘結性能。這表明制造工藝、材料選用以及涂膠工序均符合標準。
### 2. 粘結不均現象
檢測中若發現局部粘結強度不足,則需要排查相關生產環節。例如,檢查涂膠流程是否存在涂膠不均的問題,或者材料處理時是否出現雜質干擾等。
### 3. 粘結失敗或早期剝離
在動態試驗中若發生剎車片脫落或粘結層斷裂,則需要重點從材料耐高溫性能、粘合劑選擇及使用環境變化適應性等方面進行進一步分析。
## 總結與展望
剎車裝置粘結程度試驗是保證飛機剎車系統性能和飛行安全的核心環節之一。通過靜態加載、動態摩擦和環境模擬等多種方法的綜合測試,可以全面評估剎車片與剎車盤的粘結質量。這不僅有助于提升生產工藝水平,還能為后續的設備維護和改進提供可靠的數據支持。
未來,隨著航空工業的技術進步,剎車裝置粘結性能檢測將越來越齊全。例如,智能化監控系統、無損檢測設備等新技術的引入,可以更加高效地進行實時監測,從而進一步提升航空器運行的安全性和可靠性。這既是技術發展的必然趨勢,也是保障飛行安全的重要措施。
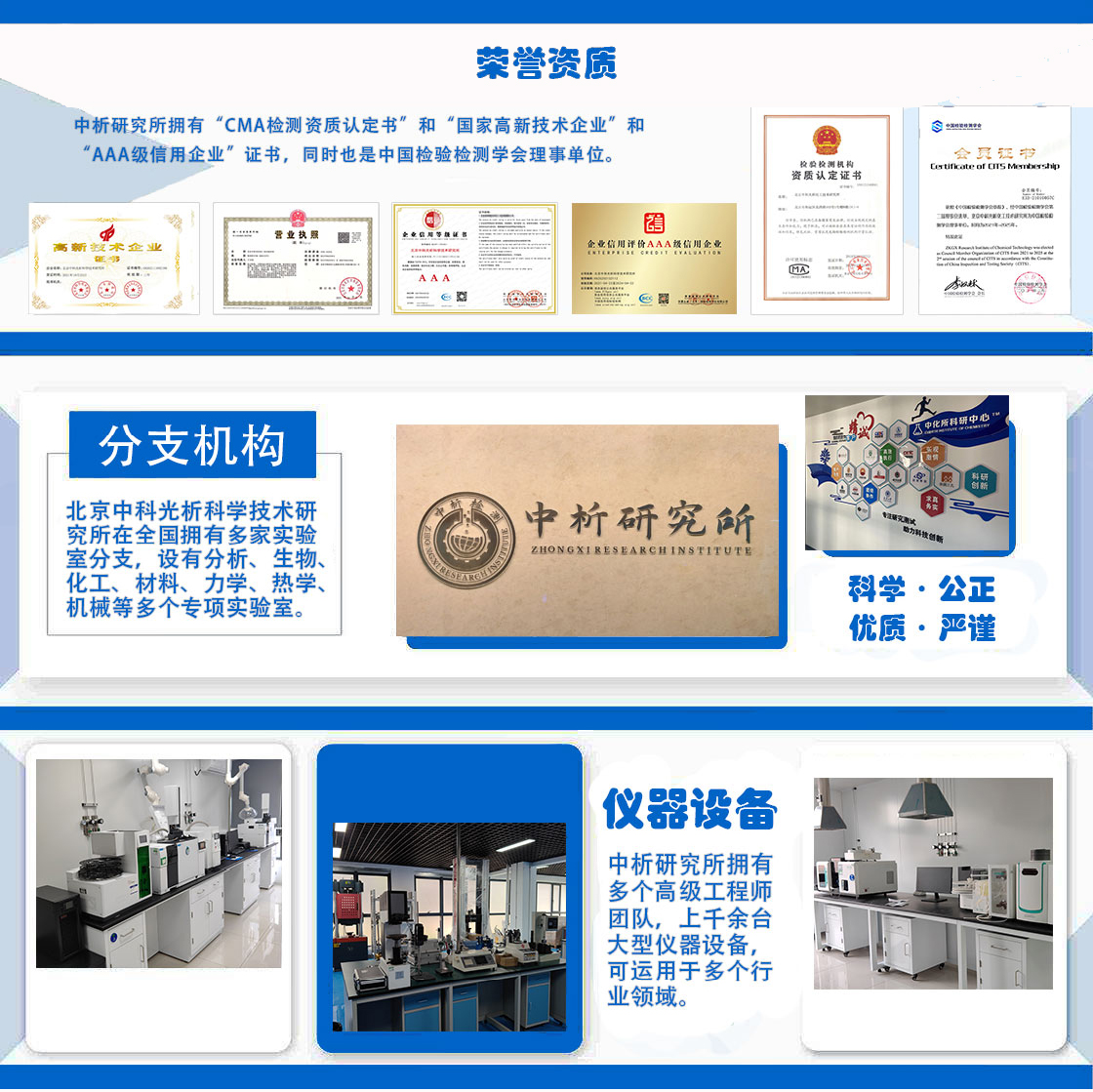
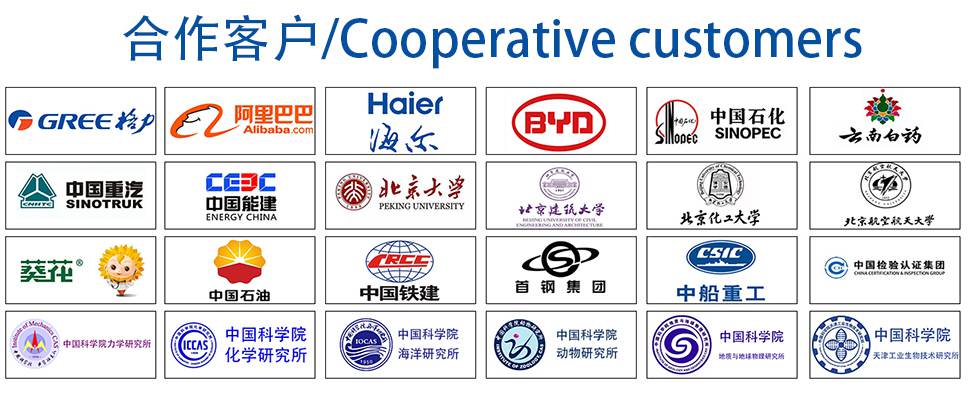