卷筒料平壓平模切機(jī)檢測(cè)
實(shí)驗(yàn)室擁有眾多大型儀器及各類分析檢測(cè)設(shè)備,研究所長(zhǎng)期與各大企業(yè)、高校和科研院所保持合作伙伴關(guān)系,始終以科學(xué)研究為首任,以客戶為中心,不斷提高自身綜合檢測(cè)能力和水平,致力于成為全國(guó)科學(xué)材料研發(fā)領(lǐng)域服務(wù)平臺(tái)。
立即咨詢聯(lián)系中化所
卷筒料平壓平模切機(jī)檢測(cè)的重要性與核心項(xiàng)目
在包裝印刷、電子材料等行業(yè)中,卷筒料平壓平模切機(jī)作為關(guān)鍵生產(chǎn)設(shè)備,其性能直接影響產(chǎn)品裁切精度、生產(chǎn)效率及材料損耗率。由于設(shè)備長(zhǎng)期處于高頻次、高負(fù)荷運(yùn)轉(zhuǎn)狀態(tài),定期開展系統(tǒng)性檢測(cè)是保障設(shè)備穩(wěn)定性和產(chǎn)品質(zhì)量的核心手段。通過(guò)科學(xué)規(guī)范的檢測(cè)流程,能夠及時(shí)發(fā)現(xiàn)模切壓力不均、定位偏差、機(jī)械磨損等隱患,避免因設(shè)備故障導(dǎo)致的生產(chǎn)中斷或次品率上升。
模切機(jī)檢測(cè)的核心項(xiàng)目清單
1. 模切精度檢測(cè):使用高精度千分尺或激光測(cè)距儀,測(cè)量模切刀版與底模的平行度誤差,確保公差范圍≤0.05mm。同時(shí)通過(guò)標(biāo)準(zhǔn)測(cè)試材料進(jìn)行連續(xù)模切,檢驗(yàn)切口垂直度與尺寸一致性。
2. 壓力均勻性檢測(cè):通過(guò)壓力分布測(cè)試膜或傳感器陣列,分析模切區(qū)域的壓力分布曲線,識(shí)別局部壓力過(guò)高或不足的區(qū)域,避免材料撕裂或切痕不完整。
3. 溫升與潤(rùn)滑檢測(cè):監(jiān)控主傳動(dòng)軸、導(dǎo)軌等關(guān)鍵部位運(yùn)行溫度,結(jié)合紅外熱成像技術(shù)分析異常發(fā)熱點(diǎn)。同時(shí)檢測(cè)潤(rùn)滑系統(tǒng)油路通暢性及油脂清潔度,確保運(yùn)動(dòng)部件磨損可控。
4. 電氣系統(tǒng)安全檢測(cè):對(duì)變頻器、伺服電機(jī)、PLC控制器進(jìn)行絕緣電阻測(cè)試與負(fù)載試驗(yàn),驗(yàn)證急停裝置、安全光幕等保護(hù)功能的響應(yīng)時(shí)效性(一般要求≤0.5秒)。
5. 材料適配性驗(yàn)證:針對(duì)不同厚度、材質(zhì)的卷筒料(如PET膜、不干膠、泡棉等),進(jìn)行動(dòng)態(tài)張力測(cè)試與收放卷同步性評(píng)估,確保材料傳輸無(wú)偏移或褶皺。
6. 機(jī)械結(jié)構(gòu)穩(wěn)定性檢測(cè):使用振動(dòng)分析儀檢測(cè)設(shè)備基礎(chǔ)框架的固有頻率,排查因地基沉降或螺栓松動(dòng)導(dǎo)致的共振風(fēng)險(xiǎn),并通過(guò)三維坐標(biāo)儀校驗(yàn)橫梁、立柱等核心支撐件的形變量。
檢測(cè)周期與數(shù)據(jù)管理建議
建議每500小時(shí)運(yùn)行后開展基礎(chǔ)檢測(cè),每2000小時(shí)進(jìn)行深度校準(zhǔn)。所有檢測(cè)數(shù)據(jù)應(yīng)建立電子檔案,結(jié)合物聯(lián)網(wǎng)技術(shù)實(shí)現(xiàn)趨勢(shì)分析,當(dāng)模切重復(fù)定位精度下降超過(guò)標(biāo)稱值15%時(shí),需立即停機(jī)檢修。通過(guò)智能化檢測(cè)體系的建設(shè),可使設(shè)備綜合效率(OEE)提升20%以上,同時(shí)降低意外停機(jī)損失。
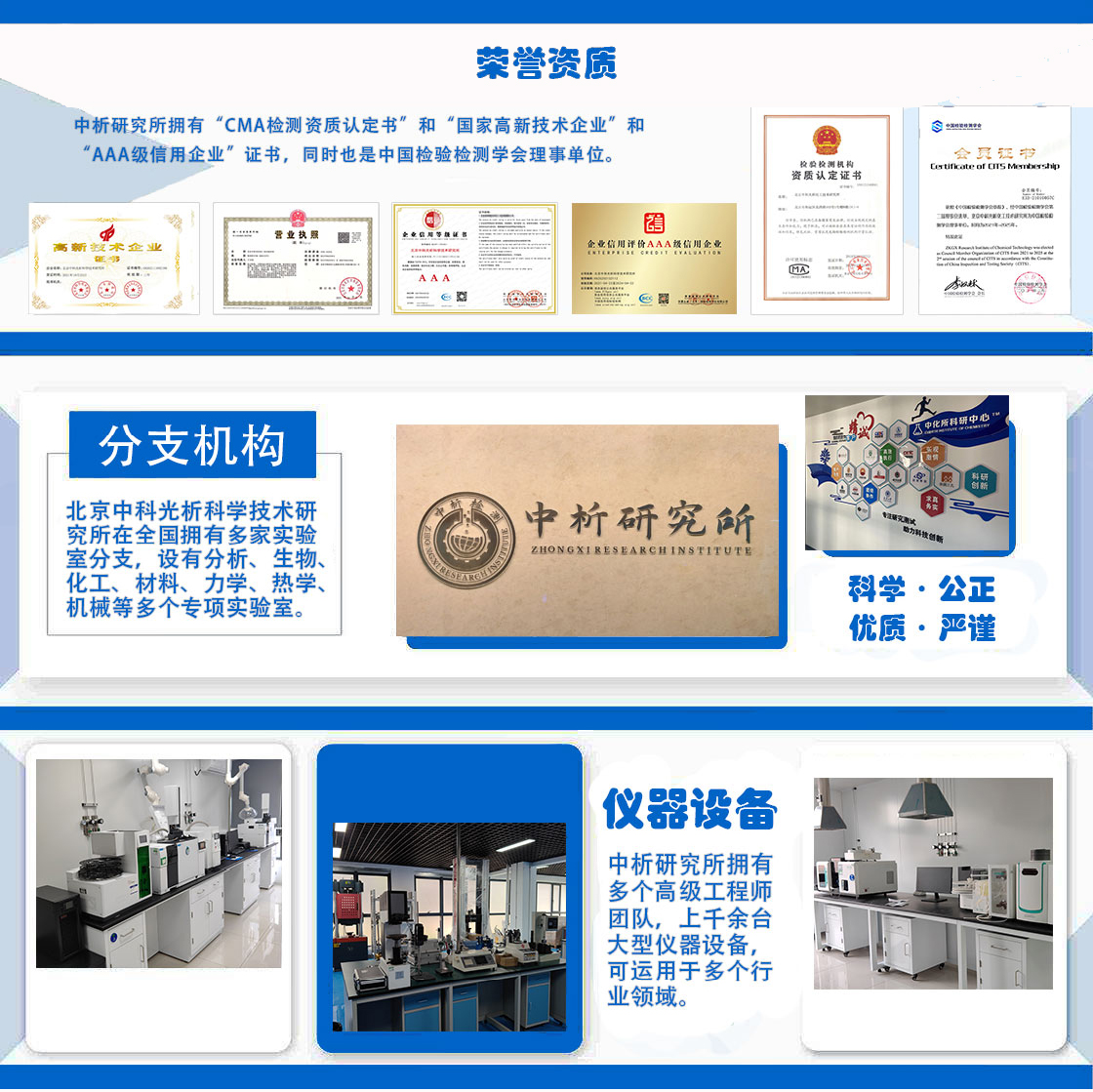
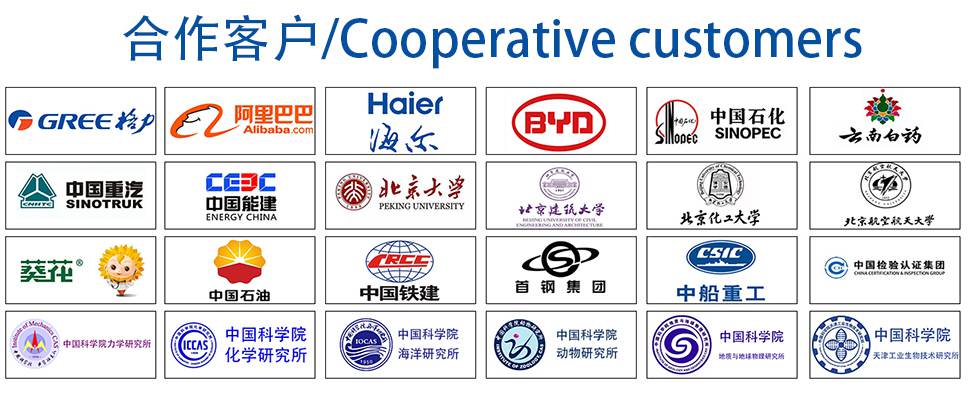